Institute News
CORREX is pleased to announce its new 3-day foundation course.
As the name suggests duration of this course is 3 days. The course has information for a new starter, experienced operative with limited experience or no desire to blast and spray and requires an ICATS card.
The foundation course does not contain any specialist blast and spray information, but concentrates on Health and Safety, tools and tool usage, preparation standards and principles, paint adhesion and application, paint faults and much more.
This course has been taken on by Hinkley C Nuclear Power Plant (EDF) and will be delivered by Cryogen (Scunthorpe). This course will be delivered to hundreds of new starters ahead of working at Hinkley C.
CORREX and Cryogen are proud to be part of this on-going ICATS training.
All enquiries to CORREX@icorr.org or kevin@paintel.co.uk
Institute News
The Institute is very pleased to announce the signing of a new 5 year agreement with the University of Manchester (UoM), to provide Student Bursaries to its Undergraduate and Post-Graduate Students studying Corrosion. This is fully in line with its Memorandum of Association – November 2020 – Section 3(b) that aims:
• To raise the standard of the scientific, technical and professional knowledge of persons engaged in or intending to be engaged in science, technology or engineering practise of corrosion and its control.
• To promote and carry out research and other scientific work in connection with science, technology or engineering practise of corrosion and corrosion control.
• To provide facilities for post-graduate courses and other studies related to the primary objects by means of research fellowships and bursaries for the remuneration, instruction and support of research graduates and students.
UoM and ICorr Relationship
The relationship between UoM and ICorr goes back several decades, with many former UoM and UMIST (Institute of Science and Technology) staff, students, and ICorr members now working in the Corrosion Industry and Academia.
The Institute has been working very closely over the past 12 months with the Academic and Administrative staff of UoM to develop the bursaries scheme. We have been hugely impressed with their commitment to the advancement of corrosion education and the dedication of its students, as witnessed first-hand at the 65th anniversary presentations of UoM corrosion teaching in April 23.
All presentations from their recent 65 year UoM Jubilee
Corrosion Symposium are now available on UoM YouTube channel: https://lnkd.in/evhHQSds.
Details of New Scheme
This new UoM bursaries scheme was championed by Bill Hedges, who has worked closely with past ICorr President Stuart Lyon, and has the full support of ICorr Council. It will start in September 2023 and provide the following for the upcoming academic year.
Undergraduate Scholarships
• ICorr will provide 4x £2,000 bursaries for undergraduate (UG) students.
• The UG scholarships will be allocated in December 2023, which is when the final year students will choose the options for the second semester, (they can choose up to 3 Corrosion units).
Post Graduate Scholarships
• ICorr will also provide 2x £8,500 bursaries for MSc students.
• By awarding the scholarships from 2023-24 academic year, the expectation is that UoM will improve the conversion rate from MSc offers to the number of people that register on the Corrosion course.
All prospective UoM corrosion course students are required to complete a detailed questionnaire in support of their application for an ICorr-UoM scholarship.
The total annual bursary support by ICorr will be £25,000 per annum. Each year UoM will review the scholarship scheme and,
if necessary, change the number and value of each scholarship, in order to maximise the number of students who select Corrosion options going forward.
New UoM Corrosion Lead
Dr Beatriz Mingo, a Royal Academy of Engineering and Presidential Fellow has recently been appointed as the new UoM Corrosion subject lead.
Beatriz of the Henry Royce Institute graduated in Chemistry (2011), completed her Masters in Materials Science and Technology (2012), and defended her PhD thesis (2016) at the Complutense University of Madrid (UCM, Spain), for which she received the Extraordinary Doctorate Award. During her PhD, she studied different strategies to improve the corrosion resistance of light alloys.
In 2013 the British-Spanish Society granted her a scholarship to complete her academic training in cutting edge 3D characterisation techniques at The University of Manchester. She also carried out two research stays at the Helmholtz Zentrum Geesthacht (2015 and 2016) in the Corrosion and Surface Technology Group, where she learned the fundamentals of active protection, with the development of self-healing coatings based on layered double hydroxides formed on aluminium based composites.
In 2016, the European Federation of Corrosion awarded her the Eurocorr Young Scientist Grant, which is aimed at promoting knowledge exchange between young and international senior scientists. In 2017, she was awarded the Humboldt Research Fellowship for Postdoctoral Researchers, and in 2018, she obtained the Presidential Fellowship at The University of Manchester.
Beatriz Mingo is currently a Senior Lecturer and Royal Academy of Engineering Fellow at The University of Manchester and Henry Royce Institute. Her research focuses on the development of environmentally friendly smart surface treatments for corrosion protection and lifetime extension of engineering systems. She has published +35 research publications in the field of Corrosion Science and her work has been recognised internationally by the European Federation of Corrosion and the International Society of Electrochemistry, amongst others. Most recently she was awarded the 2022 RAEng Young Engineer of the Year, The University of Manchester Distinguished Achievement Medal – Researcher of the Year 2022 and the UCM Alumni Award, 2022”.
The new Home for Engineering and Materials boasts a range of teaching spaces, lecture theatres, multi-purpose study areas, social spaces, and very well-equipped research laboratories.
CAPTIONS:
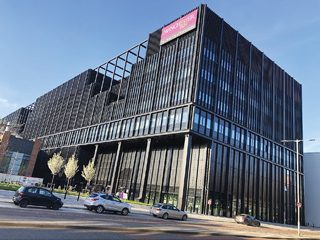
New University of Manchester Buildings – Engineering Building A.
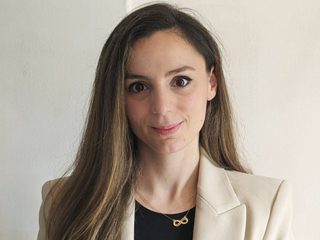
Dr Beatriz Mingo of the Henry Royce Institute Manchester.
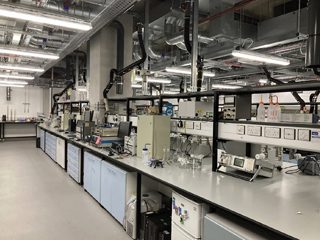
New University of Manchester Laboratories.
Institute News
During June and July, the Institute was very pleased to welcome the following new Overseas and UK Student members, many of whom joined us from our North-East Branch Sustainability Event. We wish them all every success in their future careers and ICorr journeys.
Name/University
• Narenthira Prasath Dhandapan – Newcastle University – 16 June 2023
• Long Duong – Newcastle University – 16 June 2023
• Lilibeth Urdaneta – Newcastle University – 16 June 2023
• Mohammed Aleliw – Newcastle University – 16 June 2023
• Sahish Bhosle – Newcastle University 16 June 2023
• Alfie Davies-Varnier – Newcastle University – 16 June 2023
• Chirag Padmesh Kumar – Newcastle University – 16 June 2023
• Edwin Ramirez Teljeda – Newcastle University – 16 June 2023
• Al Salamah Salim – Newcastle University – 16 June 2023
• Srivatsava Podicheti – Institute of Aeronautical Engineering (IARE) – 17 June 2023
• Jack Fergus – Falmouth University – 19 June 2023
• Mohamed Ibrahim – Newcastle University 19 June 2023
• Abhijeet Kulkarni – Newcastle University – 19 June 2023
• Ashhab Mulla – Newcastle University – 19 June 2020
• Hannah Wright – Newcastle University – 20 June 2023
• Ragav Krishnakumar – Newcastle University – 20 June 2023
• Muhammed Mansaf Maheen – Newcastle University – 20 June 2023
• Nazia Farooqui – University of Edinburgh – 20 June 2023
• Raisa Kamila – Newcastle University – 21 June 2023
• Billington Harvey – Liverpool Moore’s University – 21 June 2023
• Tamsin Dobson – University of Bristol – 26 June 2023
• Christopher Hardman – University of Bristol – 26 June 2023
• Ali Haider – University of Punjab – 02 July 2023
• Ibrahim Alhajji – King Fahd University of Petroleum and Minerals – 03 July 2023
• Leandro Liveira – University of Sao Paulo – 03 July 2023
• Saif Ramy – University of Leeds – 11 July 2023
Our Student Bursaries Scheme with University of Manchester is now approved and will commence
this September
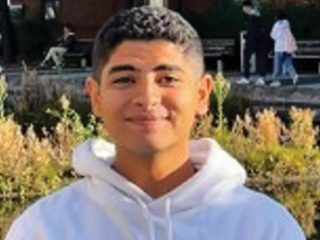
Saif Ramy, ICorr Internship Student
The Young ICorr Internship (Anne Neville Award) has also been sanctioned for support by ICorr Council at University of Leeds with additional funding kindly provided by LBBC Baskerville. The winning ICorr Student member Saif Ramy will commence his internship on 3rd July for 10 weeks. We offer our many congratulations to him and sincere thanks to Danny Burkle for arranging this and also to LBBC Baskerville for their support.
Institute News
Our Midland Branch is very active again under the new leadership of Bill Whittaker, with a full technical programme planned for the coming 2023–24 technical session. On September 14, there will be a branch meeting and visit to Manchester University Metallurgy and Corrosion group within the Department of Materials, for a tour of the brand new, state-of-the-art building. The new Home for Engineering and Materials boasts a range of teaching spaces, lecture theatres, multi-purpose study areas, social spaces, and fantastic laboratories. With a guide to the facilities from the students and corrosion teaching staff.
Event Schedule:
• Start at 3 pm: afternoon welcome refreshments.
• Lectures/talks from Midland visitors and from Manchester.
• Later, a move to the restaurant for chatting and finger food from 5:30 pm (soft and hot drinks).
• Tours in three groups of the Department of Materials, approx. 5–10 people per tour (20 minutes per tour),end 7pm.
Only 25 places available, please confirm attendance ASAP to Bill Whittaker at the midlandschair@icorr.org”
Institute News
North West Branch had a successful AGM, held at the Sherwin-Williams factory in Bolton. Special Thanks to Malcolm Morris and John Donoghue of Sherwin Williams for a fascinating tour of the facility, which produces corrosion protection and intumescent coatings applied to a wide range of structures in use today.
Institute News, Uncategorized
The branch has started a series of lunchtime webinars aimed at professionals in the corrosion industry. The first of these was held on June 8, 2023, when Kjell Wold presented “Technology of Corrosion and Erosion Monitoring”, and the feedback was overwhelmingly positive.
Kjell Wold, a corrosion expert with over 30 years of experience, gave a comprehensive overview of the latest technologies for corrosion and erosion monitoring. He discussed the different types of monitoring methods, the benefits of each method, and the challenges of implementing these methods in the field.
Kjell also discussed how high-accuracy UT data can be used proactively for process optimisation in addition to integrity management. He gave several examples of how this data has been used to improve the performance of pipelines.
The webinar was very informative, Kjell was an excellent presenter, and he was able to keep the audience engaged throughout the presentation. The Q and A session was also very informative, and audience thoroughly enjoyed it.
The webinar series continued on July 13, 2023, with our fellow committee member, Ennery Leon, presenting “Cathodic Protection: Field Tests and Troubleshooting.”
Ennery has more than 17 years of experience in the petrochemical, steel-making, and oil and gas industries, and is currently the Upstream Asset Integrity Team Leader at TAQA Global in the Netherlands. He detailed the field testing that can be used to evaluate the performance of a coating and CP system, eg, structure-to-electrolyte potential, CIPS, ACVG, PCM etc.
He also shared some tips and tricks from his experience in CP troubleshooting.
The branch held a summer social event to bring together the local corrosion community, with the object of growing the branch’s engagement and membership, on June 29, 2023, at the Tower of London, and it was considered a great success. The event was well-attended by around 40 professionals, including some of the branch committee members, and the atmosphere was festive. We are grateful to our committee member, James Lawson, for organising the event, and to Carboline for sponsoring it.
The tour of the Tower of London was well-organised and informative. Our guide was knowledgeable and engaging, and did a great job of bringing the history of the Tower to life. We learned about the different uses of the Tower over the centuries, from a royal residence to a prison, to a place of execution. We also had a private tour of the Crown Jewels which was amazing to see.
Guests then enjoyed a delicious dinner at the Tower, followed by the Passing of the Keys ceremony, which was a highlight of the evening. It is a centuries-old tradition that takes place every night at the Tower of London. The ceremony involves the Chief Yeoman Warder locking the gates of the Tower and delivering the keys to the Constable of the Tower.
The ceremony is full of pomp and circumstance, and it is a truly memorable experience. We were able to watch the ceremony from a privileged vantage point, and we felt like we were part of history.
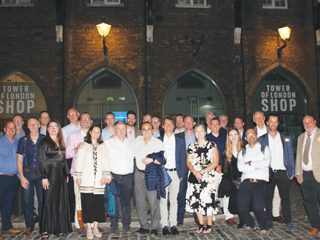
Some of the attendees.