Institute News
The 22nd International Corrosion Congress, is a prestigious global event dedicated to advancements in corrosion science and engineering and was held on 22nd to 26th October 2024 in Xi’an, China.
Organised by the International Corrosion Council (ICC) and supported by the Chinese Society for Corrosion Protection (CSCP), the congress brought together corrosion experts, scientists, engineers, and industry leaders from around the world. The event aimed to share the latest research, technological innovations, and sustainable practices in corrosion management across many different industries.
The Institute of Corrosion (ICorr), represented by President Stephen Tate and Vice President Dr. Yunnan Gao, attended the congress upon the invitation from the CSCP and the congress organisers, as providing international support to this congress and following ongoing ICorr/CSCP discussions during the previous 12months. The congress featured a diverse program of keynote presentations, technical sessions, workshops, and networking opportunities. Topics ranged from enhancing corrosion controls and corrosion management procedures to new digital tools and artificial intelligence for corrosion monitoring and mitigation. Xi’an, known for its rich history and role as a cultural hub, served as an inspiring venue for this landmark event and attracted a large audience.
During the Congress, ICorr Presidents actively engaged in discussions with the leadership team of the International Corrosion Council (ICC), including ICC past president Prof. Dr. Günter SCHMITT President (2018-2021) from Germany, ICC President (2021-2024) Prof. Emma ANGELINI from Italy, ICC President Newly Elected President in Xi’an (2024-2027) Prof. Vngaranahalli Srinivasan RAJA from India and ICC President Elect (2027-2030), Prof. Dr. Zehbour PANOSSIAN from Brazil.
The ICC Congress provided an excellent platform for ICorr to showcase its initiatives and contributions to corrosion science. ICorr leaders shared insights on professional development programs, such as training and certifications, and emphasised the organisation’s dedication to advancing corrosion engineering standards globally.
ICorr’s participation at this congress greatly enhanced its mission to contribute to global advancements in corrosion control and its aspiration to promote knowledge exchange and innovation within the international community. The interaction between with the ICC leadership emphasised ICorr’s growing influence outside of the UK and reinforced its commitment to strengthening ties with international counterparts.
The ICorr presidents’ successful joint participation in the Xi’an conference highlighted the growing interconnectivity and shared purpose of the global corrosion community. It also set the stage for a future defined by mutual support between CSCP/ICC/ICorr and welcome advancement in knowledge sharing.
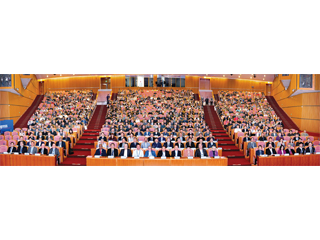
Photo: All Attendees of the Opening Ceremony of the 22nd ICC Corrosion Congress in Xi’an. ICorr Presidents: Right 3 and Right 5, 2nd Row, Central Block.
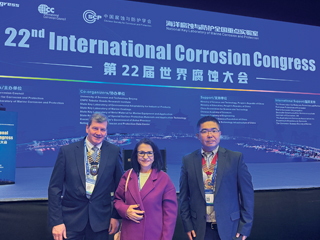
Photo: ICorr Past and Future Presidents and ICC
President Elect (2027-2030), Prof. Dr. Zehbour
PANOSSIAN from Brazil, during the Congress.

Photo: ICorr Past and Future Presidents and ICC Presidents and
Congress VIPs at the Congress Dinner.
Institute News
Each year the Institute of Corrosion bestows a range of internationally renowned awards in recognition of excellence in corrosion science and engineering and to reward outstanding service to the Institute and the wider corrosion community. Many of these awards are open to nomination by both members and non-members of the Institute. Below is a brief description of each award, together with details of how to nominate potential candidates.
U.R. Evans Award
The U.R. Evans Award is the premier scientific award of the Institute of Corrosion and is presented annually for outstanding international achievements in pure or applied corrosion science. The recipient is selected by a Corrosion Science Division panel and presented with an engraved sword at the annual Corrosion Science Symposium (CSS). The symposium is one which seeks to encourage the participation of the junior members of the corrosion community who would appreciate the visit of, and address by, a corrosion scientist of international repute.
The form of the award symbolizes the fight in which we are all engaged. The recipient is also granted Honorary Life
Fellowship of the Institute. Nominations may be submitted at any time via email to the CSD Chair, Julian Wharton (j.a.wharton@soton.ac.uk).
Prof David Shoesmith (University of Western Ontario, Canada) was presented with the U.R. Evans Award 2024 by Stephen Tate (ICorr President) at the 65th Corrosion Science Symposium, which this year joined Electrochem2024 at Manchester Metropolitan University, held between 11th and 13th September. In his plenary talk entitled ‘Corrosion of the Spent Fuel Waste-form and Engineered Barriers in a High-Level Nuclear Waste Repository’, David addressed how various intricate electrochemical investigations into the possible long-term corrosion processes within Canadian/Swedish/Finnish deep geological repositories. This was a very fitting commemoration for the centenary of the first publication of Corrosion of Metals by Ulick Richardson Evans in 1924.
Paul McIntyre Award
The Paul McIntyre Award recognises a distinguished senior corrosion engineer who has demonstrated excellence not only as a leading practitioner in the field but also in fostering European collaboration and advancing international standards. This prestigious award includes an engraved trophy, presented at the annual CED Working Day meeting. The recipient will be invited to deliver a short presentation of their professional contributions and is encouraged to submit an article for publication in Corrosion Management. We’re also excited to announce that the 2024 award winner will be revealed at the upcoming CED Working Day on Corrosion Awareness Day on 24th April 2025. Nominations for the 2025 award are now open and should be submitted to the CED Chair, Danny Burkle, at Danny.Burkle@lbbcbaskerville.co.uk by the end of July 2025.
T.P. Hoar Award
The T.P. Hoar Award is presented to the authors of the best paper published in the scientific journal Corrosion Science during the previous calendar year. The winning paper is selected by a sub-committee of the Corrosion Science Division and the authors receive a certificate and a cash sum of £400.
Galloway Award
The Galloway Award is presented to a student author for the best publication describing original research in corrosion science and engineering as judged by a sub-committee of the Corrosion Science Division. The student should be the primary author of the work and preferably first author. A summary of the winning paper is published in Corrosion Management and the prize consists of a certificate and a cash sum of £300. The Institute does not retain copyright of the material, so this does not prevent separate publication of the work in a scientific journal. Submissions (in the form of a paper published within the past 12 months or a draft publication) may be sent via email at any time to the CSD Chair, Julian Wharton (j.a.wharton@soton.ac.uk). Supervisors may nominate students.
Lionel Shreir Award
The Lionel Shreir Award is given to the best student presenter at the annual Corrosion Science Symposium. Selection of the recipient is carried out by a sub-committee of the Corrosion Science Division. The award consists of a certificate and a cash prize of £125.
The Shreir award in 2024 was presented to Amber Sykes (University of Leeds). Amber gave an excellent presentation linked to her PhD research into the evolution of porous FeCO3 layers, and their influence on the CO2 corrosion rate of carbon steel.
For further details on the Institute awards, including lists of past recipients, please visit https://www.icorr.org/icorr-awards/
Institute News
Report by Sue Wharton, Science in Parliament (SIP) – The Journal of the Parliamentary and Scientific Committee (All-Party Parliamentary Group).
On 15th October 2024, visitors including eleven delegates from ICorr, were welcomed to the discussion meeting by George Freeman MP, new Chair of the P and SC.
The Parliamentary and Scientific Committee is an All-Party
Parliamentary Group funded by Membership – for further details go to
www.scienceinparliament.org.uk
Stephen Tate, President of ICorr, introduced Institute activities; training and informing corrosion engineers at all levels is a key objective. Courses are run, qualifications awarded, specialised meetings held, and financial support given, including for their Young Engineer Programme (YEP), currently running in London.
The APPG then heard four specialist presentations: Gareth Hinds, Senior Fellow and Science Area Leader, Electrochemistry Group at the National Physical Laboratory, gave us his thoughts on ‘Raising Awareness of Corrosion’; David Parker, Environmental Consultant, spoke on ‘The Potential of Value Retention Processes (VRPs)’; Izabela Gajewska, Intertek CAPCIS Consultancy Services, gave us her ideas on ‘Mentoring the Next Generation towards Corrosion Prevention’; and finally Christian Stone of Loughborough University and Concrete Preservation Technologies Ltd, described ‘Advanced Corrosion Management Techniques to Reduce Cost and Risk in Our Built Environment’.
Corrosion costs the UK £80 billion per year. Professor Hinds stressed we must raise awareness of this; we have expert knowledge of corrosion control practices, which could save up to 35% of this total. All countries pay the price of corrosion, and the World Corrosion Organisation (WCO), of which he is currently President, promotes global education and best practices in corrosion control; tackling corrosion also fits well with UN Sustainable Development Goals. Ideally, corrosion control should be incorporated in designs for new projects; unfortunately, undergraduate courses tend not to specialise in the subject, with knowledge generally learnt on the job.
David Parker focused on re-use, explaining the concept of Value Retention Processes (VRPs), Refurbishment and repair, re-use, and remanufacturing were reviewed. Benefits from re-use include reduced emissions, saving raw materials, and more skill orientated jobs. Industry and services are aware of benefits but hampered by regulatory and trade barriers and cost pressures.
Izabela Gajewska, Intertek CAPCIS Consultancy Services, and an ICorr Young Engineer, gave us her views on developing the new generation of corrosion engineers.
Optimised corrosion prevention practices can improve safety, protect the environment, and save money. She listed the varied work of corrosion professionals, reiterated the shortage of new engineers, and suggested suitable courses; experienced specialists retiring impacts the transfer of knowledge. Better communication on education, training, and mentoring would enable and encourage more homegrown students. Christian Stone described advanced corrosion management techniques. Much of our built environment uses reinforced concrete, but mid-20th century public infrastructure can now require intervention; current repair strategies are often lacking and work delayed due to budget constraints. Refurbishment of existing structures is better than rebuilding. Britain is a world leader in corrosion surveying and management; electrochemical surveys pinpoint issues and tailor them to specific locations. Hybrid Galvanic techniques are UK inventions, used worldwide. Recent Reinforced Aerated Autoclave Concrete (RAAC) concerns have been tackled using specific survey methods and anodes, now protecting many public buildings.
A varied Q and A session discussed RAAC safety, reluctance to use new technology, and shortage of specialist engineers. Reactive attitudes persist; only when a collapse occurs do organisations have to rethink. Better communication and design are needed; short-termism is a false economy.
A national register of structures at risk in all areas is considered desirable. Corrosion engineers can play an important role in sustainability and climate change; there should be more awareness of the value of their skills.
The Institute of Corrosion expresses its special thanks for assistance provided to ICorr by Karen Smith, Leigh Jeffes, Roger Brown and Sue Wharton of the Science in Parliament (SIP) Group.
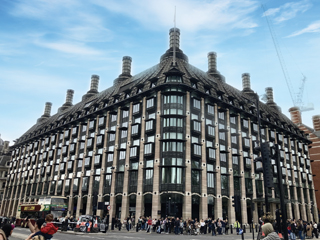
Photo: P and SC Portcullis House, London. Image Courtesy of Parliamentary and Scientific Committee APPG.
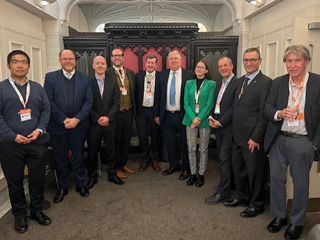
Photo: L-R Yunnan Gao (ICorr Vice President), George Freeman MP (Past Minister of State in the Department for Science, Innovation and Technology), Gareth Hinds (Past ICorr President/Speaker), Christian Stone (ICorr Speaker), Stephen Tate (ICorr President/Speaker), Stephen Benn (3rd Viscount Stansgate), Izabela Gajewska (ICorr Speaker), David Parker (ICorr Speaker), David Mobbs (Coatings Specialist) and Douglas Mills (Past ICorr Technical Secretary). Image Courtesy of Parliamentary and Scientific Committee APPG.
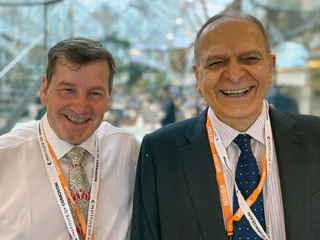
Photo: ICorr President Stephen Tate with ICorr MIC Tutor Tony Rizk. Image Courtesy of Parliamentary and Scientific Committee APPG.
Institute News
On 21st November 2024, the ICorr Young Engineers Programme (YEP) reached its grand finale with a vibrant presentation evening hosted at the Institute of Corrosion London Branch. The event, led by Danny Burkle and Izabela Gajewska, marked the culmination of months of effort by participants, mentors, and organisers. It was a night to celebrate technical brilliance, teamwork, and innovative thinking in the field of corrosion science. The YEP has been a foundation of ICorr’s commitment to developing future leaders in the corrosion industry, providing early-career professionals with opportunities to develop their skills, engage with industry experts, and tackle real-world engineering challenges.
The event was not just a competition but a celebration of innovation, teamwork, and professional growth. The evening also provided an excellent networking platform, connecting young professionals with industry experts.
The Event – 2024 YEP Final Case Study Presentation
A total of 24 early-career professionals from leading organisations participated in this year’s programme. This year’s case study challenge centred around a real-world failure of dump condenser heads at a power station, requiring teams to identify root causes, propose solutions, and develop long-term mitigation strategies.
The six teams presented their findings to a panel of experienced judges, each bringing a unique perspective to the evaluation. The judging panel included Stephen Tate, Gareth Hinds, Madeleine Davidson, and Chris Williams. Their collective expertise ensured that the participants received insightful feedback, enhancing the educational value of the programme.
A highlight of the evening was the keynote speeches delivered by Izabela Gajewska and Stephen Tate. Izabela talked about the Importance of Corrosion Management, drawing attention to the staggering global cost of corrosion—estimated at $2.5 trillion annually (£90B within UK)—and the critical need for effective collaboration, education, and risk management strategies to mitigate these impacts.
Stephen Tate followed with an inspiring message, reflecting on the YEP’s vital role in advancing the field of corrosion. He highlighted how the programme fosters innovation, builds professional confidence, and develops the leaders of tomorrow.
Programme Achievements: This year’s programme was a testament to YEP’s growing impact. With over 60 applications, the highest ever, and extensive engagement on social media generating 10,000+ interactions, the programme continues to draw attention from the global corrosion community. Since its inception in 2009, YEP has trained over 100 early-career professionals, equipping them with the tools and knowledge to excel in their careers, many of these YEP graduates are now actively participating within ICorr.
Recognising Excellence: The Winners
The culmination of the evening was the announcement of the winners. Team 1, mentored by Ali Morshed, took the top honours for their comprehensive and innovative approach to the case study challenge. The team consisted of Álvaro González Fuentes, Amy Johnstone, Ben Hudson and Kishan Nittur Ramesh, whose outstanding teamwork and technical analysis set them apart.
In addition to the team award, Rochelle Holness was recognised as the Winning Individual for her exceptional technical contributions and presentation skills. Rochelle’s dedication and leadership earned her a coveted place in the AMPP Leadership Programme, where she will represent ICorr at the upcoming AMPP conference
in Nashville. Mentors provided invaluable guidance to participants, helping them navigate the technical and practical challenges of the case study. The mentors included: Ali Morshed, Rob Doggett, Chris Googan, Stephen Shapcott, Andrew Sturgeon and Shengqi Zhou.
Acknowledgements
Special thanks were extended to the mentors, judges, and ICorr experts who contributed to the programme’s success, including individuals such as Stephen Tate, Yunnan Gao, and others and, our event sponsors BP, AMPP, Wood Thilsted, Intertek CAPCIS and LBBC Baskerville.
Looking Ahead
The 2024 ICorr YEP Final Presentation Evening was a resounding success, highlighting the importance of nurturing the next generation of corrosion professionals. Congratulations to all participants, particularly the winners, Team 1 and Rochelle Holness, for their remarkable achievements. A comprehensive report on the evening, featuring detailed insights from the presentations and feedback from the judges, will be published in the upcoming issue of Corrosion Management. Stay tuned for more on the outstanding work showcased during this unforgettable evening.
Join the Young ICorr Committee
Young ICorr is currently looking for new committee members. This is a fantastic opportunity for early career engineers, scientists, and researchers in the field of corrosion to get involved, gain experience, and make valuable connections. If you are interested, please contact Young ICorr for more information at icorryep@gmail.com

Photo: Winning Team Presenting.

Photo: All YEP Participants and Organisers.

Photo: YEP Winning Team: Team 1. Left to Right: Yunnan Gao, Kishan Nittur Ramesh, Amy Johnstone, Ali Moshed, Álvaro González Fuentes, Ben Hudson.

Photo: Standout Individual
– Rochelle Holness.
Institute News
It is with sadness that we must report the death in August 2024 of J D Griffiths, aka ‘Dave Griff’. Dave was a coating inspection and quality management expert who contributed hugely to the Institute of Corrosion coating inspector training and certification scheme.
He worked with R J P (Ran) Nicklin, who led one of the larger coating inspection specialists in the 1970’s.
In the early 1980s, Dave formed J D Griffiths and Associates Ltd, an independent firm of specialist engineers providing quality control, advisory and inspection services within the corrosion control and structural and piping steelwork protective treatment industries. Dave and his colleagues provided specialist expertise in respect of coatings and linings within the marine, oil, gas, petrochemical, product storage, transportation, pipeline and power generation sectors. They provided these services internationally, throughout the United Kingdom, Norway, Italy, Holland, France, Spain, Germany, Saudi Arabia, Libya, Jordan, the United Arab Emirates and Mexico.
Dave also provided independent expert witness and opinion services in cases of technical and commercial disputes, typically between asset owners and contractors.
In later years, much of Dave’s time was working with Argyll Ruane Ltd (ARL) who were the delegated body operating the Institute of Corrosion coating inspector training and certification scheme and later also the cathodic protection technician and engineer training and certification scheme. Dave was the Scheme Manager, reporting to the ICorr Governing Board (later formed into the Professional Development and Training Committee, recently deleted) and was often treading a very difficult line of ‘working for 2 masters’, both ICorr and ARL. He dealt with these challenges with professionalism and honesty.
ARL’s key competences related to non-destructive testing (ultrasonic, radiographic etc) and for many years Dave was the prime source of coating expertise as required within the ICorr Scheme. He also worked closely alongside John Thirkettle and
Chris Lynch who wrote the early CP courses, along with the other CP tutors, to assist in the delivery of the ICorr CP Scheme.
The Institute owes a considerable debt to the professionalism and dedication that Dave brought to his role as Scheme Manager. He was a significant contributor to the foundation of our scheme.
He will be missed by his wife Jacqui.
A personal note from Brian Wyatt:
Dave was a long-term friend and respected colleague. He was
also a man of integrity and of considerable fun. He was the first person I knew with a ‘radio phone’ in his car (yes, a radio phone,
pre mobile phones); great for calling the operator to book a
decent restaurant……
We travelled together to Libya to work on one of his projects;
I blame him for choosing the route via Malta on what I termed a ‘cattle ship’; it was most definitely a dual service vessel. It took
me 6 months to recover from the chest infection; I took advice
from both our excellent Vet and GP…
The negotiation, that took the time of single escalator ride, of the long-term arrangement whereby ICorr and ARL (who at that time were managing the delivery of the CP courses for us) agreed a commercial arrangement with the CPA for them to promote our courses into their industry. The CPA are the steel in concrete Corrosion Prevention Association, who remain to this day an important
partner for our ICorr CP Training and Certification work in concrete.
I remember his kindness and courtesy to all, even when vexed.
He will be missed by me and many others in ICorr and beyond.
Photo: J D Griffiths, Aka ‘Dave Griff’.
Institute News
Stephen Shapcott CEng FIMMM FICorr AWeldI, London Branch member, Past Young Engineers Programme recipient and now mentor, and Vice Chair or AMPP UK Chapter, has been awarded this year’s Smeaton Medal in recognition of his work in the scale up and deployment of material solutions for next generation low carbon energy sustainable chemical process technologies.
The Institute of Corrosion is also very pleased to announce that Stephen has additionally been recognised as a newly elected fellow of the institute.
When asked about these two notable events in his career occurring in such close succession, Stephen said, “To be a fellow of the Institute of Corrosion has been a careerlong goal and so to be awarded the Smeaton medal just the week before has been a fabulous experience. I hope any success I have had will inspire the next generation of Corrosion Engineers such as those on the Institute’s Young Engineers Programme.”
All in ICorr offer their congratulations to Stephen on this magnificent double win.
Stephen, who is Head of Materials Engineering – Licencing for Johnson Matthey’s (JM) Catalyst Technologies Licensing Business, was nominated by Dr Elizabeth Rowsell OBE CChem FRSC, JM’s CTO, for his ability in leading the selection of materials of construction for a wide variety of extreme chemical environments, facilitating the safe deployment of world scale chemical and energy process technologies. The development of these processes has resulted in multiple patent applications.
The origins of the Smeaton medal date from the 1970s. The current, third series of medals has been commissioned by the Smeatonian Society of Civil Engineers to commemorate the 250th anniversary of the formation of the society in 1771. The third series is intended to recognise engineers in the early or mid-stage of their careers who have demonstrated outstanding engineering achievement in the management of hostile environments, such as windstorms, earthquakes, the human body, space, cyberspace, the deep oceans, or under extreme chemical, biological, or nuclear conditions.
The award of the medal to Stephen was announced at the society’s luncheon held at the University of Leeds on the 30th of October 2024 to mark 300 years since Smeaton’s birth and was presented by HRH The Princess Royal, who is an Honorary Member and past President of the Smeatonian Society.
Further information regarding the current series of
Smeatonian Society awards and past winners can be found
at the following website:
https://www.smeatonians.org/smeaton-medal


Photo: Stephen Shapcott with Her Royal Highness Princess Anne for the Smeaton Medal Presentation at the University of Leeds, on the 30th of October 2024.

Photo: Guests at the Annual Luncheon of the The Smeatonian Society of Civil Engineers.

Photo: Stephen Shapcott with Johnson Matthey’s CTO Elizabeth Rowsell Who Nominated Him
for the Medal.