Institute News
IMechE Argyll Ruane (IAR) have recently announced a successful management acquisition, marking a significant milestone in the organisation, which is a world leader in Coatings and Non-Destructive Testing (NDT) and Coatings training, examinations and NDT consultancy services.
Building on its strong brand and heritage, the company will reinstate its former name Argyll Ruane Limited (ARL), which it used from 1998 – 2016. Members of the management team, proudly led by Managing Director Bryan Ravenshear, bought the two trading entities IMechE Argyll Ruane and IMechE Fife NDT Limited, from the Institution of Mechanical Engineers (IMechE).
The new owners, Bryan Ravenshear (Managing Director), Sally Taylor (Finance Business Partner) and Kristian Hampson (Group Technical Manager) are excited to advance the organisation’s legacy of success. Bryan Ravenshear, Managing Director, commented:
“Kristian, Sally and I have dedicated many years to working in various roles and departments within the organisation. We possess a deep understanding of its operations, the industries
we engage with, and the clients we support, positioning us well for future success. With our team’s ongoing support, we firmly believe that Argyll Ruane Limited will continue to be a trusted partner in the NDT and Coatings industries and providing support to ICorr for many years to come.”
As the Institution of Mechanical Engineers (IMechE) embraced a revised strategic direction, an extensive review was conducted of the enterprises within Professional Engineering Projects Limited, the Institution’s commercial arm. The goal was to ensure that these enterprises aligned with the Institution’s updated vision and strategic objectives and to assess whether the current ownership is conducive to fostering continued growth and success. The review concluded that, through having greater autonomy and adopting a more commercially focused ownership, IMechE Argyll Ruane (IAR) would be able to better leverage its strong market position and the many opportunities available
operating as Argyll Ruane (ARL) globally. If you have any questions about the acquisition, please contact the team:
enquiries@argyllruane.com
Contact Details:
Argyll Ruane Limited,
4 Europa View, Sheffield Business Park,
Sheffield, S9 1XH Tel: (+44) 114 399 5720
Source:argyllruane.com
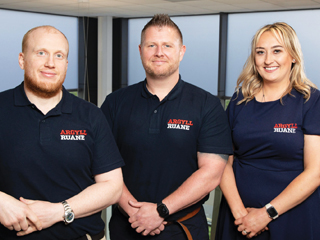
Photo: New proud owners of Argyll Ruane Limited: Kristian Hampson
(Group Technical Manager), Bryan Ravenshear, (Managing Director) and
Sally Taylor (Finance Business Partner).
Institute News
The Professional Assessment Committee (PAC) is responsible for the evaluation and assessment of applications for professional membership of the Institute of Corrosion (TICorr, MICorr and FICorr), and consists of a Chair, a Vice Chair and at least 5
other members.
All-volunteer members of PAC are expected to be professional members of the institute and to have extensive experience in various disciplines within the corrosion industry or academia. Members of the committee may be nominated by any ICorr Member and are ultimately appointed by the PAC Chair. The normal term of membership is 4 years, although any member approaching this is eligible for re-nomination. The Chair is also awarded on a 4-year basis, with the option for re-nomination by Council.
The PAC’s terms of reference are to assess applications for professional membership in compliance with Equality, Diversity, and Inclusion (ED&I) requirements, including unconscious bias. All information provided by the applicant is treated with the utmost confidentiality and is not discussed or passed on to any third party in accordance with the Data Protection Regulations. Applications are checked for compliance with the Membership Regulations for education, training, and experience as appropriate to the grade and must be accompanied by two references, at least one of which should be from a Professional Member of the Institute.
Applications for Professional Membership are sent to 3
members of the PAC Committee (providing they are not also acting as a referee) for assessment and recommendation of suitability for Professional Membership at the grade appropriate to their experience. Where unanimous approval is not
received, the PAC Chair adjudicates (with the assistance of the President if considered necessary) and recommends whatever action or consultation is considered appropriate. Successful candidates are announced in Corrosion Management, unless requested otherwise.
The members of PAC only meet, either in person or online, at the discretion of the Chair. In general, communication is carried out by email or post, with the applicant’s files only retained for record purposes at Head Office.
All applicant’s information and assessments are treated as confidential and held in the member file in the head office and retained for up to 5 years upon leaving the institute.
Anyone interested in joining PAC as a professional assessor should contact the current chair, Paul Lambert, via email
at pac.chair@icorr.org. The positions of both Chair and
Vice Chair are due for renewal in 2025, and any interest
in taking up either of these roles should also be directed
to Paul.
Institute News
You may have heard or read that there are some changes to Construction Skills Certification Scheme (CSCS) cards due at the end of this year, December 2024.
Refer Industry Accreditation Renewals Close | Official CSCS Website

The strategic direction of the revised CSCS scheme is designed to mirror that of industry and help facilitate a fully qualified workforce going forwards.
Please note that this does not apply to our cards as we are in a different category along with another ‘NVQ’ scheme. Our cards are valid for the foreseeable future.
We do have some exciting changes coming in April of 2025 though. I have been in discussions with CSCS regarding our changes that are being dealt with by myself and the CORREX team. We will be announcing smarter cards in line with our respective courses and the use of mobile phones for the same usage, in the near future. CORREX will make another announcement soon to you.
Regards
Kevin Harold
CORREX Managing Director
CORREX Ltd
Corrosion House
5 St Peters Gardens
Marefair
Northampton NN1 1SX
T: + 44 (0)1604 438222
E: correx@icorr.org
W: www.icats-training.org
Kevin Harold
Institute News
Dear Members,
Welcome to the September/October issue of Corrosion Management.
The overall theme of this issue is the “Application of Artificial Intelligence (AI) and Machine Learning (ML) in corrosion management”.
E Tolsma-de Klerk and L F Curado have jointly authored the first technical article, “The Challenges and potential of AI in asset integrity management.” They have discussed the history, implementation, and challenges of using AI in asset integrity management (AIM).
Our second article, “Unleashing the power of AI: corrosion prevention revolutionised,” is written by Muhammad Hussain and Tieling Zhang. The authors have explained the application of AI and machine learning in corrosion prevention, predicting corrosion rates, evaluating corrosion inhibitors, and corrosion monitoring. The article discusses predictive maintenance and proposes that AI can improve the ability to anticipate failures and can optimise corrosion control.
The third technical article, “Practical application of AI in steel corrosion analysis,” written by Shahrizan Jamaludin and Md. Mahadi Hasan Imran, focusses on the use of AI in analysing steel corrosion, especially in areas like reinforced concrete, atmospheric corrosion, and pitting corrosion of stainless steel.
Following on from recent complaints of the Paris Olympians, we have a special article “Why do bronze medals tarnish so quickly?” by Dr. Roger Francis. This article explains the corrosion mechanisms behind the tarnishing of bronze medals. Dr. Francis has described various environmental factors and human factors that cause the tarnishing of medals. Practical solutions to reduce tarnishing
of medals are also provided.
We sincerely welcome all your contributions and encourage you to share your content and local observations / case studies for consideration. This includes industry news, technical articles, and photos for our “Corrosion Around Us” feature. We would also be delighted to receive further submissions for our “Ask the expert”, “Corrosion Morphologies” column and “Fellow’s Corner.” We look forward to your valuable contributions.
With kindest regards,
Dr Shagufta Khan, FICorr
Consulting Editor, editor@icorr.org
Institute News
Dear Members,
October will be a very special month for the Institute as we welcome Dr Jane Lomas to the Surface Treatment Scheme Manager (STSM) role and Brenda Peters as the Institute’s new Honorary Secretary. We are very pleased that John Fletcher will remain as a valued member of ICorr Council and thank him for all his previous support to us.
This past month saw ICorr well represented also at EuroCorr24 in Paris and also at Electrochem24 in Manchester through our Corrosion Science Division. We offer our congratulations to all the award recipients at these events.
We had some further good news during September when we received a visitation from the Engineering Council to our Northampton HQ and following a thorough review of our organisation, we are delighted to announce to award to ICorr of a provisional license to offer Eng.C C registrations (CEng, IEng and EngTech) from the UK Engineering Council (Eng.C) to our valued members. This new direct scheme will be implemented from January 2025. We are most grateful to our new volunteer assessors who have joined us from across the UK and overseas to help us with our scheme launch and to Anthony Setiadi for coordinating these assessor activities. Most importantly to David Harvey for his fantastic leadership over the past 2 years of Eng. C. scheme development.
Our newly strengthened CPGB / STGB Cathodic Protection and Surface Treatment governing boards are now up and running, and we very much welcome the participation of YICorr and former YEP winners on both these and on our ICorr branch committees, they are doing splendid work and helping build the future of the Institute. The current YEP programme with 24 candidates is now drawing to a close after some excellent lectures throughout 2024, many thanks to all our volunteer presenters. Our readers are reminded of the ICorr 2024 YEP – Final Presentation of Case Studies, to take place on 21st November 2024 15:30 – 21:00 at: Lancaster Hall Hotel, Craven Terrace, London, W2 3EL hosted by ICorr London Branch. All are welcome to attend this. Do please contact Danny Burkle should you have any queries on YEP activities danny.burkle@lbbcbaskerville.co.uk
During August we held our very successful 2024 Annual Corrosion Forum (ACF) kindly hosted by ENGTEQ Aberdeen on 27th August 2024, on the theme “Corrosion Management in the Energy Sector” with over 60 attendees from across the energy industry. With many congratulations to the Aberdeen Branch for organising this most successful event.
Our new MoU with AMPP has now been completed, which will
bring more joint events during 2025 and 2026. Work continues developing other ICorr collaboration opportunities in China, India,
and the Middle East.
Please do get involved in our upcoming activities and keep an eye
on the ICorr Events Calendar at: www.icorr.org/events/
Do note for your diaries, the upcoming Institute AGM to which all ICorr members are cordially invited. This will be an ‘In-person’ Event at: Neville Hall, Westgate Road, Newcastle Upon Tyne NE1 1SE on 13th November 2024 with an associated NE Branch Offshore Wind Technical Program.
Enjoy the Autumn and new ICorr technical sessions ahead of us from our eight regional branches which now include Central Scotland and Wales and South-West.
With my very best wishes.
Stephen Tate,
President: Institute of Corrosion
president@icorr.org
Institute News
Following successful events in partnership with Manchester University, including the recent World Corrosion Awareness Day event, NW Branch plans to hold their AGM in Manchester on Tuesday 1st October. The AGM will feature presentations, including one from Paul Lambert, ICorr PAC Chair on the 200th anniversary of Sir Humphry Davy’s invention of cathodic protection. For further information refer: Sir Humphry Davy (1778–1829) | Royal Institution (rigb.org) and All About Cathodic Protection & Electrochemical Corrosion (icorr.org)
The AGM agenda will cover the minutes of the previous meeting and the election of local branch committee members. Food and refreshments will be provided for attendees. Final details of exact timings and the venue are to be confirmed.
Anyone wishing to get involved with the branch, join the committee or make a presentation at future meetings should contact nwchair@icorr.org
ICorr North-West Committee (Left to Right): Izabela Gajewska, Kathy Brook, Paul Lambert, Brenda Peters, Greg Brown and Jane Lomas.