The cart is empty!
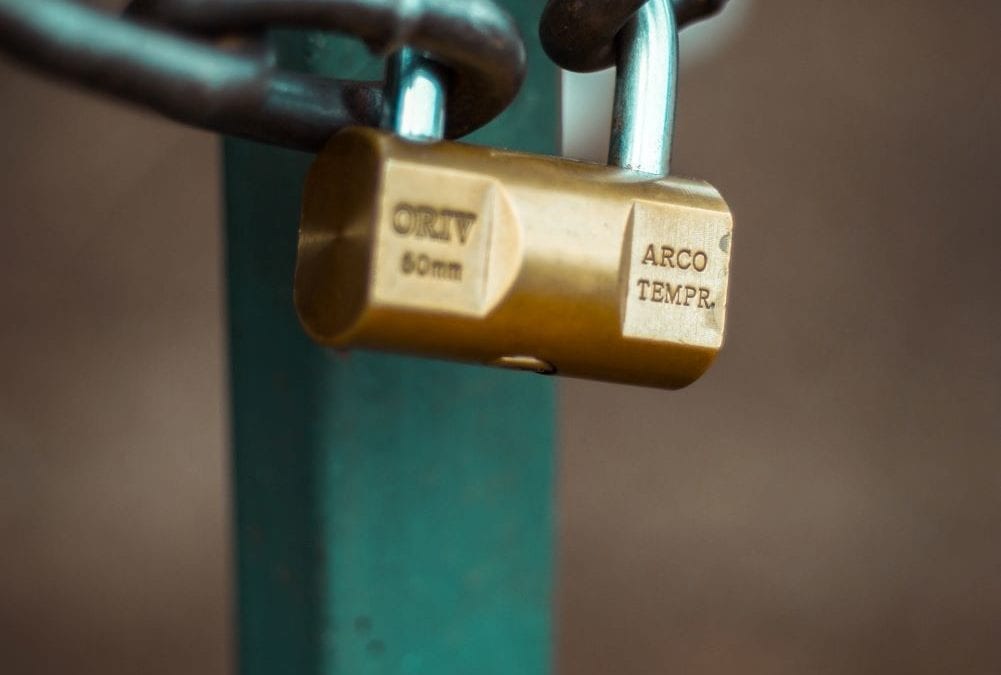
Unlocking and Managing the Effects of Corrosion
Fundamentals of Corrosion Explained
The effects of corrosion include the ultimate destruction of possessions and products (if the product is left untreated) and a real but hidden financial cost. That cost of corrosion is passed onto consumers and businesses – and it’s colossal.
A two-year study by NACE put the corrosion cost at $2.5 trillion each year, or around 3% of global GDP. The study also estimated that implementing best practices in corrosion prevention could result in as much as $875 billion in savings. Imagine the positive effect that releasing this cash could have on world economic growth.
In this article, we briefly discuss the fundamentals of corrosion – the who, what and how of corrosion management.
Who is affected by the effects of corrosion?
There is not a single life on this planet that is not affected by corrosion. Of course, those in developed countries suffer a greater direct impact, but corroded metals seep into the earth, rivers, seas and air. As do chemicals and other hazardous materials which escape because of corrosion in pipes and tanks. Eventually this pollution goes global.
Even more serious than the cost of corrosion is the impact it has on our safety. The effects of corrosion of steel reinforcing bars in concrete can lead to collapse of buildings, bridges and roads. Corrosion of components in planes, trains and automobiles can have disastrous consequences.
Energy and utility companies are in a constant battle against corrosion, with the effects of corrosion causing disruption and cost from drilling platforms to domestic pipelines.
Corrosion causes financial costs, health and safety issues, and loss of life. It’s unsightly and depletes the world’s natural resources.
At the forefront of corrosion prevention are engineers, paint inspectors, designers, technicians and scientists. Engineers in civil, mechanical and naval fields are continually assessing potential or actual corrosion and incorporating anti-corrosion measures into their projects and work strategies.
What are the mechanisms of corrosion?
Classification of the type of corrosion present is commonly made on one of the following three factors:
- The nature of the corrosion (immersed or atmospheric)
- The mechanism of the corrosion (electrochemical or chemical reactions)
- The appearance of the corrosion (uniform or localised)
There are many techniques and tools that are used to help in the detection and classification of corrosion. Eight common forms of wet corrosion can be identified by their appearance:
- Uniform corrosion (when the entire surface is corroding at the same rate)
- Pitting corrosion (small holes in the metal)
- Crevice corrosion (corrosion that occurs in the gap between two adjoining surfaces)
- Galvanic corrosion (corrosion of one metal preferentially to another with which it is in electrical contact)
- Erosion corrosion, including cavitation and fretting (degradation of a metal due to the relative motion of a corrosive fluid)
- Intergranular corrosion (localised corrosion along the grain boundaries of a metal while the bulk of the grains remain unaffected)
- Dealloying (occurring in certain alloy metals, in which the alloy metal loses its reactive element and retains the corrosion resistant element)
- Environmentally assisted cracking, such as stress corrosion (cracking caused by tensile stress in a corrosive environment)
To identify some of these types of corrosion, you may need to use advanced techniques such as optical or electron microscopy.
How can you manage corrosion?
There are five principal strategies in corrosion prevention:
1. Selection of materials
Some metals are highly resistant to corrosion (such as gold and platinum), while others have a low resistance to corrosion (like sodium and magnesium).
By using appropriate metals (or alloys) for specific use and environment, engineers can increase the life of products. Their cost is obviously a very important factor in this decision.
2. Inhibitors
Some chemicals act to inhibit corrosion. These include silicates, phosphates, nitrites, and organic amines. Inhibitors are generally preferred in closed systems where the presence of the inhibitor can be more easily maintained (for example in heating and cooling systems towers).
3. Coating
Coating isolates the metal from the corrosive environment surrounding it. The coating may be metallic (for example, tin-plated steel). They may also work like galvanised steel in which the coating corrodes in preference to the metal beneath. Coatings are commonly non-metallic, such as paint, and may be either organic or inorganic.
4. Cathodic protection
Cathodic protection works by applying an external electrical current so that the corrosion reaction takes place on a separate surface to the metal to be protected, with electrons forced to flow to the metal that is to be protected.
5. Design
Designing products and structures to eliminate or minimise the potential for corrosion helps to reduce maintenance and repair costs and time; for example, by designing structures with fewer crevices in which corrosion often develops.
Obtain Professional Membership of ICorr with ‘Fundamentals of Corrosion’ training
For all who want to expand their career opportunities or wish to expand or refresh their knowledge of corrosion, the Institute of Corrosion offers the five-day Fundamentals of Corrosion for Engineers Course. Successful completion of the course is required to obtain Professional Membership of the Institute of Corrosion if you don’t have either formal qualifications in corrosion or relevant experience.
The interactive course takes place in a classroom format. During the first four days, your time will be occupied by talks and practical sessions. On the last day, there is a short review and an examination. In the course, you will learn:
- Basic corrosion science and corrosion mechanisms
- The electrochemical series and its practical uses
- Corrosion prevention and management methods
- The basics of cathodic protection
- Surface preparation challenges, paints and coatings
- Corrosion and environmental conditions
- The basics of material selection and design
- The basics of corrosion testing and monitoring
Presented by Dr Jane Lomas, a corrosion and coatings engineer with more than 30 years corrosion experience, and guest presenter Dr Les Callow, a metallurgist and corrosion engineer with more than 40 years of corrosion experience across multiple industries, this course redefines training standards in fundamentals of corrosion.
For more information and dates of upcoming Fundamentals of Corrosion courses, click here.
Places on this course are strictly limited to 10 people. To ensure you are not disappointed, download the booking form and email it to admin@icorr.org today.