The cart is empty!
Hot Dip Galvanizing Inspector – Online
Hot Dip Galvanizing Inspector – Online
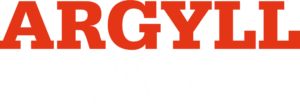
Course Overview
Online course designed to assist candidates in gaining the skills and knowledge to inspect Hot Dip Galvanized steel products
Hot-dip galvanizing is a process commonly used to provide long-term protection to steel products from corrosion. Hot-dip galvanized steel requires a thorough inspection of the finish product to ensure compliance with relevant specifications.
Approved by the Institute of Corrosion (ICorr) and produced with the assistance of the Galvanizers Association, this Level 2 course will help students to gain the knowledge to inspect hot-dip galvanized steel products and gain an industry recognised qualification.
The course assumes all candidates hold ICorr Painting or Protective Coating Inspector approval (any level), or lent, and therefore have some knowledge of inspection philosophy. Some corrosion and coating knowledge is also important due to the large amount of corrosion problems which have arisen.
Course content
Developed by industry specialists, the content is segmented into 4 modules. With interactive elements and end-of-module assessments, the course accommodates various learning styles, fostering knowledge retention and effectively preparing you for the ICorr Hot Dip Galvanizing Inspector Level 2 examination.
Online Modules:
- Hot Dip Galvanizing Overview
- The Galvanizing Process
- Coating Faults
- Inspection and Testing
Key topics covered include:
|
|
Learn on our online platform
Why learn online?
- Our user-friendly online platform enables you to complete this course from anywhere in the world
- Learn in your own time, at your own pace
- View course content as many times as you like prior to examination
- Access to all training materials on the platform for up to 6 months.
- Less time out of work
- Save on accommodation costs
- Save on transport costs
Course pre-requisite
Candidates are required to:
1 |
Have a knowledge of inspection philosophy, surface preparation, anti-corrosion coatings and how to use common inspection instruments. |
2 |
Hold an ICorr Protective Coating Inspector (or equivalent) certificate and ideally hold a minimum of 12 months’ coatings related experience. Equivalent certifications include:
|
3 |
Seek advice if hold less than 12 months’ coating experience as they may still undertake the course and become certified once relevant experience has been obtained. Course can be taken for knowledge only without an examination. |
Qualification
The course is accredited by the Institute of Corrosion (ICorr). On successful completion of the course and relevant coatings related experience, candidates will become a certified Level 2 Hot Dip Galvanizing Inspector.
The certificate is valid for 5 years and can be renewed online prior to expiry.
Book Now
Follow the steps below to book onto our online Hot Dip Galvanizing Inspector Level 2 course.
1 |
Complete our enquiry form to book > Ensure you submit all relevant documentation outlined on the application form to facilitate a speedy process! |
2 |
Enquiry review Your enquiry will be reviewed and a member of our team will be in touch. Payment information will be sent once full eligibility criteria has been met. Upon receipt of payment, your booking will be processed, and login details will be sent via email to gain access to our online platform. |
3 |
Online platform access Access our online platform anytime, anyplace*, for up to 6 months. Learn the training material at your * Note: Access requires a good internet connection. |
4 |
Examination Once you have completed the training material, contact the team to book your remote examination. We are flexible with exam availability and do our best to work around you. The examination is conducted remotely and comprises of multiple choice questions across 3 papers. It typically takes approximately 4.5 hours to complete, including rest breaks. The examination is marked instantly. |
5 |
Post-examination On successful completion of your examination, your result will be processed and submitted to the Institute of Corrosion (ICorr). ICorr will issue your certificate and wallet card, which will be valid for five years. This will be sent to you directly from ICorr. Please note that certificates can take up to 10 weeks to arrive. |
Interested in this course?
Contact the Arygll Ruane team if you have any questions about this training course.