ICorr Aberdeen Updates
On Thursday 7th November 2024 the Aberdeen Branch in a joint meeting with TWI welcomed Dr. Cheng Huan Zhong of Inductosense Limited, with a talk entitled ‘A Pathway to Thickness Measurement Locations (TMLs) Digitalisation.’
Complimentary to the recent presentation to South-West Branch by Erik Fabre this event focussed specifically on Case Studies of Inductosense Applications globally.
Cheng Huan received a B.Eng. degree in mechanical engineering and a PhD. degree from University of Bristol, England, in 2015. From 2015 to 2016, he was a Research Associate in the non-destructive testing research group at the University of Bristol. Both his PhD and Research Associate work was focused on the development of passive wireless transducers for structural health monitoring. He is a
co-founder of Inductosense Ltd, an industrial spin-off from Bristol University in 2015 and the Chief Technology Officer. He has managed multiple product development projects such as sensors, handheld data collector and remote data collector.
A Pathway to Thickness Measurement Locations (TMLs) Digitalisation
Synopsis: Permanently installed sensors provide more accurate results compared to conventional inspection due to their consistent positioning and coupling. However, due to their cost, they are normally used for monitoring critical areas for corrosion rate estimation. There are hundreds of thousands of thickness measurement locations (TMLs) on a process site for piping and vessels, making it challenging to monitor all of them. Inductosense has proposed an alternative approach that combines passive sensors and a different data collection method to enable a cost-effective, consistent, and deployable solution with wide sensor coverage possible at low cost.
Dr. Zhong presented their handheld data collector, robotics, and online solutions and demonstrated how they work together to address different applications with accessibility and inspection frequency. The presentation concluded with a large number of case studies aiming to demonstrate the benefits of this approach.
Amongst applications included were:
- Buried Pipeline Monitoring
- Drones
- Erosion Monitoring
- Integrated Corrosion Management
- Manual Wands
- Overhead Pipework Monitoring
- Production Optimisation
- Remote Data Collectors
- Riser and Flowline Monitoring
- Robots and Crawlers
- Ship Tank Usage
- Specialised Vessel Monitoring
- Subsea ROV Data Collectors
The Event provided interesting opportunities for questions.
Please contact the Aberdeen Chair for details of future ICorr Aberdeen Events.
ICorr Aberdeen Joint Online Meeting with TWI
On Tuesday 24th September 2024 the Aberdeen Branch held a joint online meeting with TWI and welcomed Neil Gallon, Principal Engineer of Rosen, with a talk on Welding and Metallurgy Requirements for Hydrogen Service.
Having previously worked for various consulting and manufacturing
companies, including British Steel Tata Steel and GE Wellstream. Neil’s, current work with ROSEN UK concentrates on understanding the effects of gaseous hydrogen on steel properties.
Neil outlined the requirements for
material selection, welding, and metallurgy of carbon steels for gaseous hydrogen service. He also described
the mechanisms and effects of gaseous
hydrogen embrittlement, presented current code requirements in terms of material properties (including welding), and gave an overview of recent research and code developments.
Key Points
Hydrogen embrittlement is the detrimental effect of hydrogen on the mechanical properties of metals and alloys.
-
The fundamental feature that drives much of the integrity concerns and challenges in gaseous hydrogen pipelines is the absorption of atomic hydrogen within the steel microstructure. The interactions of hydrogen can lead to major degradation of mechanical properties such as strength, durability, fracture toughness, and fatigue crack growth rate. These have been studied by various researchers of material types used in repurposed pipelines, such as API Series 5L X42, X52, X65, X80 and X100.
-
The data available to date, is not comprehensive but all show that all performing properties are reduced by increasing levels of Hydrogen.
-
While hydrogen pipelines could be purpose-built, it is very likely that a major proportion of the future transmission network will revolve around the integration of existing natural gas or other hydrocarbon infrastructure. Hydrogen pipeline design codes tend to be more constraining or restrictive than that for hydrocarbons. For example, typical hydrogen standards will limit the use of steels up to API 5L X52 (L360) to tackle hydrogen embrittlement issues, while over 45% of the European NG system is designed with higher steel grades.
-
The Code for Hydrogen pipeline integrity ASME B31.12 lists pipeline materials suitable for hydrogen transportation. Material compositions and properties are more restrictive than “standard” API 5L requirements on items such as the Charpy shear area requirement, the Maximum YS and UTS (including AWT) and a more restrictive chemical composition. The implications are that additional manufacturing and purchasing restrictions will be necessary and existing natural gas pipelines for repurposing may not meet material requirements. From a design perspective and materials performance factor, hydrogen pipelines will operate at lower pressure than that of natural gas unless specific hydrogen test data (KIH) is available.
-
A Material Hardness maximum of 248HV is required for production testing, which is even more severe than sour service requirements.
-
The magnitude of the interaction of hydrogen and steel is determined by the specific nature of the steel microstructures and chemistries, not just the grade. This important facet puts a great emphasis on the understanding of materials ‘DNA’ and on testing. Microstructure performs an important role in achieving higher fracture toughness in the presence of gaseous hydrogen up to 20.7 M Pa and alloy processing design influences final steel microstructure formation.
Mechanism of Hydrogen Embrittlement in Steels
Hydrogen embrittlement is basically the loss of ductility of a metal resulting from the adsorption of Hydrogen.
- Adsorption of H2to the steel surface.
- Dissociation of H2molecule.
- Absorption of H atoms into metal matrix.
-
Diffusion to thermodynamically favoured sites e.g. crack tips, dislocation cores, grain boundaries.
- Actual embrittlement takes place (mechanism unknown).
Hydrogen pipeline integrity depends on material susceptibility, stress, and environment. The possibility of cracking is largely dependent on the environment, and susceptibility to HE is dependent on the amount of hydrogen available. The equilibrium concentration of hydrogen in the metal depends on the partial pressure of hydrogen (Sieverts’ law) and its diffusivity (Fick’s law). At room temperature, H concentration from gaseous hydrogen is very low.
Neil outlined the effect that hydrogen has on pipeline integrity in terms of the principal properties of strength, durability, fracture toughness, and fatigue crack growth rate.
Hydrogen has a relatively small effect on strength at transmission pipeline pressures, while its effect on ductility is more dramatic; this has implications for fracture toughness. Laboratory studies of the effects of internal hydrogen and surface absorbed hydrogen on tensile strength and ductility demonstrate this slight fall in UTS in charged environments, but dramatic loss of ductility from 18 down to ~3% strain levels.
It is also clear that hydrogen reduces toughness from lab studies, but there is large variability in results, possibly due to microstructural differences in pipe grades.
Testing Approaches
There are two main approaches for testing H effects on fracture toughness:
-
Rising load fracture toughness as recommended by ISO 11114-4. This produces a measurable toughness value J, K, CTOD; however, the fracture toughness depends on H kinetics, and the results depend on loading rate.
-
Threshold stress intensity factor KIH – recommended by ASME B31.12 and ISO 11114-4. The results do not depend on H kinetics. However, on the downside, this is a pass-fail outcome, has long testing time with several tests required, and the result is not quantitative.
www.nist.gov/image/materialstestinghighpressurehydrogentestchamberjpg
Studies have also been made of fatigue crack growth rates in hydrogen environments:
-
As yet, there are currently no agreed standard test protocols, but full-scale tests are currently ongoing, and there is currently a lot of research activity in this area.
-
Crack growth da/dt is realised in the laboratory conditions, although there is no evidence that it has happened in pipelines in service, so the implications for pipelines are unknown.
-
Crack propagation does not happen all the time; it appears to be due to the pre-conditioning and stress state around the crack tip, with unpublished evidence that sometimes cracks arrest.
In summary, the requirements for material selection, welding, and metallurgy of carbon steels for gaseous hydrogen service are developed, but there remain areas for further study and development:
- Codes are not mature enough to follow prescriptively.
-
No clear relationship between in-air and in-hydrogen material properties.
-
Likely that extensive programmes of material qualification in gaseous hydrogen will be required.
-
Significant amounts of current code developments and research are necessary.
An extensive Q&A followed this well-attended online event, and the Aberdeen ICorr committee offered its thanks to Neil on following his most informative presentation.
The Aberdeen Branch provides a very full technical programme of both in-person and online events. Abstracts of potential papers for the Aberdeen Technical Programme are always welcome for consideration, and anyone wishing to present should correspond soonest with the 2024/2025 Chair and Technical Programme Co-ordinator: meilingcheah@gmail.com
Further information about the Aberdeen Branch and past presentations may be found on their website page: Aberdeen Branch – Institute of Corrosion. https://www.icorr.org/aberdeen/ under Local Technical Programme and to join the Aberdeen Branch mailing list, please contact: icorrabz@gmail.com
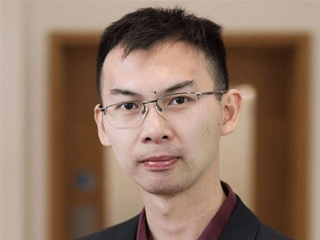
Presenter: Dr. Cheng Huan Zhong.
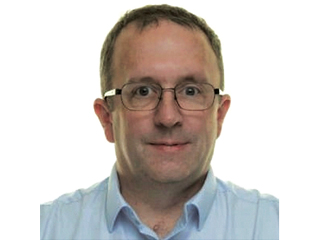
Neil Gallon, Principal Engineer
of Rosen.
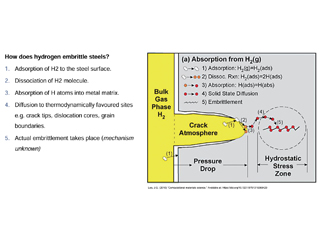
Photo: Explanation of Hydrogen Embrittlement Process.
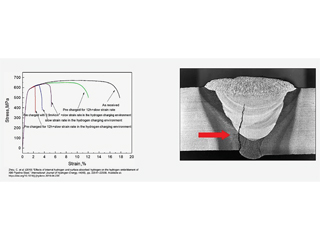
Figure 1: Effects of Internal Hydrogen and Surface-Absorbed Hydrogen on Hydrogen Embrittlement.
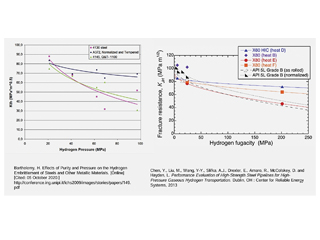
Figure 2: Effects of Purity and Pressure on Hydrogen Embrittlement.
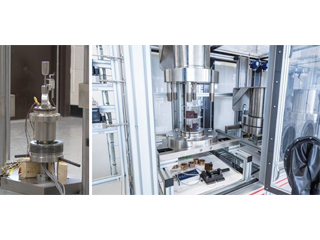
Photo: NIST High Pressure H2 Test Chamber.