The branch held its final webinar of the summer on 14th September, when Esteban Amiranti, Business Development Manager at CM BEASY Ltd., presented “Corrosion Data Management, 3D Digitalisation and Digital Twin.”
The first technical session of the 23/24 season was held on 12th October at branch’s usual venue, the Lancaster Hall Hotel, Bayswater, when Simon Daly, a consultant with Safinah Group in Gateshead, gave a presentation on “Increasing the use of sensor technology to monitor coating performance.”
Simon’s current role involves providing consulting services to clients, ranging from specification writing assistance through failure investigations and root cause analysis to providing expert opinions to their energy and infrastructure clients. He has a B. Eng. (Hons.) degree from the University of Leeds as well as qualifications in marketing and international sales management. He is an AMPP-certified Senior Corrosion Technologist and a professional member of ICorr, with over 30 years’ experience in the protective coatings field.
Simon explained that recent years have seen significant improvements in the use of remote sensors for the measurement of corrosion, and also for categorising the corrosive environments in which facilities operate. Access to remote sensing has never been more important since the restrictions imposed on many assets during the COVID 19 pandemic, but with the benefits come challenges. The paint industry has been brought up with the human eye as the primary means of condition surveying. Simon posed the question “Will sensors ever be able to replace the flexibility and detail this ultimate sensor technology can provide?”
His presentation focused on the use of sensor technology to remotely determine coating performance in service. The topic of Corrosion Under Insulation (CUI) was used to highlight some of the features and benefits of coating performance sensors, compared to other types of sensors focusing on the presence of moisture or the loss of wall thickness.
Sensor technology is ideally suited for areas where the paint condition/level of corrosion cannot be seen. Examples of this includes immersed areas, inaccessible internal surfaces, inaccessible external surfaces such as beneath insulation, and areas where the risk to humans of surveying is too high.
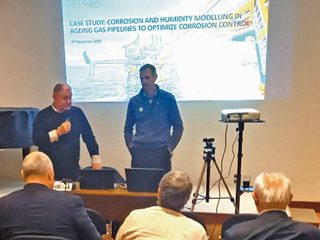
Simon Daly presenting his talk on ”increasing the use of sensor technology
to monitor coating performance.”
Using CUI as an example we can see that we can continuously measure:
• The driver – the presence of moisture in the insulation which may ultimately give rise to a corrosive environment which causes the issue.
• The cause – the time of wetness and the coating condition are both critical in contributing to ultimate failure.
• The consequence – a loss of wall thickness resulting in reduction in fitness for service.
Historically, measurement of different parameters to determine the integrity of the paint film has required visual observations and/or direct contact, but in the case of insulated service this is not possible, so we must rely on the sensor technology alone to tell us what is going on beneath the insulation and cladding, this presents a specific challenge in terms of introducing such a technology to the marketplace in terms of establishing the necessary high degree of confidence in the technology.
Simon then considered what a potential validation of such systems could look like to address the issue of confidence required to replace historic visual inspection much favoured by safety practitioners and regulators, and what might be some of the challenges encountered along the way?
There was a lively discussion on the floor, Simon was thanked for his talk, and presented with an ICorr pen.
At the November technical meeting, Steve Hodges, Intertek, gave a presentation on “The application of CO2 corrosivity, and humidity, modelling to gas pipeline internal corrosion management.”
Steve is a Chartered Engineer and a member of the Institute of Materials Minerals and Mining. He has a B.Eng. (Hons.), Materials Science and Engineering, University of Wales, Swansea, and an MSc in Corrosion Science and Engineering, from UMIST. He started his corrosion career in NZ undertaking corrosion consultancy and contract research before joining CAPCIS (now Intertek CAPIS), in Manchester. Over a 20-year period Steve has consulted to the oil and gas, petrochemical, mining, and power generation industries in some 18 countries, and was a guest lecturer on Corrosion Management and RBI on the University of Manchester’s MSc course for 8 years. He works predominantly in the areas of: corrosion modelling, corrosion/integrity management, materials selection, and fitness for service.
Steve Hodges presenting on “the application of CO2 corrosivity, and humidity, modelling to gas pipeline internal corrosion management.”
Steve’s presentation was essentially a case study of the assessment of a selection of pipelines that formed part of a network of 1000’s of km of gas and gas condensate pipelines, and some lessons learned from this.
While there were many similarities to the pipelines in the field network, the ‘one size fits all’ corrosion management approach in place had not been adequately controlling internal corrosion, as evidenced by historical in-line inspection data. A series of studies were undertaken combining both CO2 corrosion rate modelling (including basic flow modelling) and humidity modelling, along with analysis of historical operational and intelligent pig data.
In some instances, there were cost savings to be made with the cessation of batch corrosion inhibitors, in others, more onerous controls were required. However, the main takeaway from this series of studies was that the pipelines, though notionally the same, could not be considered as one in terms of degradation or corrosion management.
After the Q and A session, Steve was thanked for his talk, and given an ICorr pen as is usual for London Branch speakers.
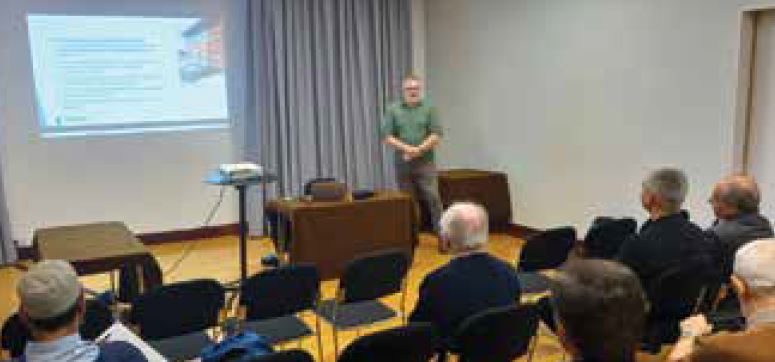