The cart is empty!
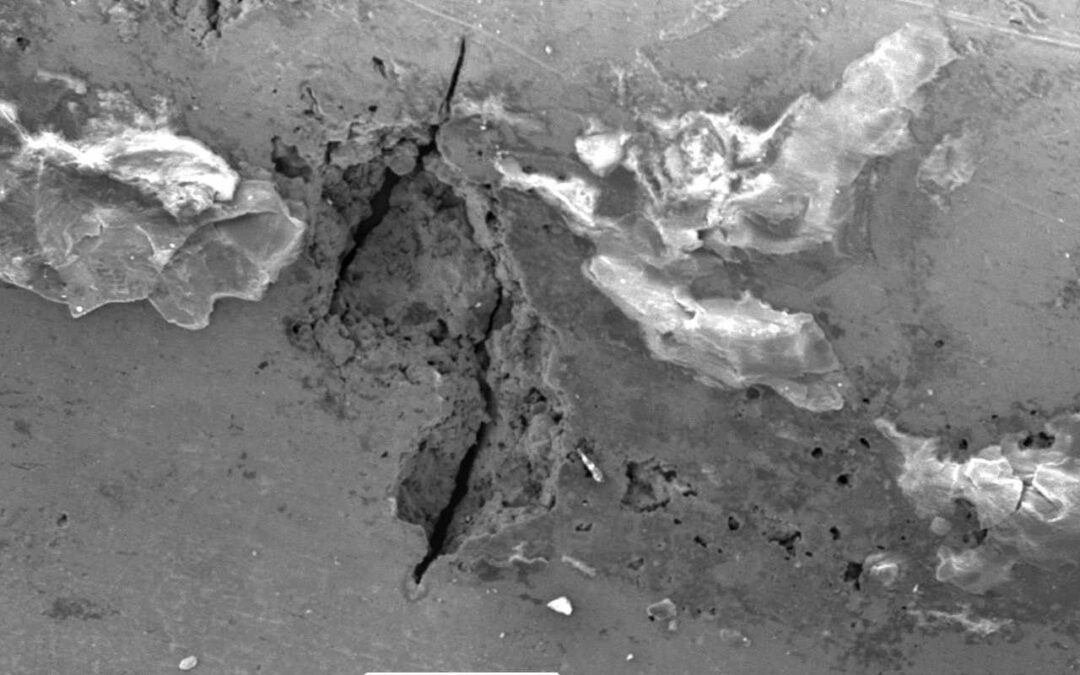
The CED Working Day and Symposium – Corrosion Prevention in the 21st Century:
Learning from the past to protect the future, will be held on 27th April at NPL Teddington.
The final programme has now been confirmed:
09:30 Registration & Welcome drinks
10:00 Welcome & Introduction – Danny Burkle (LBBC Baskerville)
10:15 Introduction to NPL and NPL Activities – Gareth Hinds (NPL)
10:30 Understanding Localised Corrosion and how this can improve corrosion prevention methods – Alison Davenport (University of Birmingham)
11:00 The corrosion of canisters during interim storage and deep geological disposal of radioactive waste – Cristiano Padovani
/James Hesketh (Jacobs)
11:30 Lunch & Working Group Discussions
12:30 Paul McIntyre Award Presentation – Stephen Tate (ICorr President)
12:45 Applying materials experience from
oil and gas production to carbon capture
and storage – Steve Paterson (Arbeadie Consultants Ltd)
13:15 How to Make Trends and Influence People – Jonathan Mann (Jacobs)
13:45 NPL Laboratory Tours and Refreshments
14:30 The limits of use of copper alloy and stainless steel heat exchanger tubes – Roger Francis
15:00 Benefits of using corrosion protection for offshore wind – Anthony Setiadi
15:30 Closing Discussions – Danny Burkle (LBBC Baskerville)
15:45 End
For further details, please see leaflet in this issue, or scan this QR code to reserve your place.
CED Working Day and Symposium
The Corrosion Engineering Division invites you to join our annual working day and symposium on Thursday 27th April, 2023. The theme of this year’s symposium is, “Corrosion Prevention in the 21st Century: Learning from the past to protect the future.”
This one-day meeting will be the latest in a series of recent working days of the Institute of Corrosion’s Corrosion Engineering Division. The meeting will be held in person at the National Physical Laboratory (NPL), Teddington. This year’s meeting is wide ranging and covers ‘Corrosion Prevention in the 21st Century: Learning from the past to protect the future.’
After the technical talks and tour of the facilities and laboratories on site at NPL, the meeting will break up into the individual CED working groups. Where possible, agendas for the working group meetings will be published separately in advance on the CED website
(http://www.icorr.org/about_icorr/technical_divisions.phtml).
In addition to the technical talks and a tour of NPL, the 2023 Paul McIntyre Award will be presented.
The working day is a fantastic opportunity to network with other corrosion professionals from a range of different industry sectors; and, to learn about how corrosion prevention techniques can help preserve equipment and infrastructure occurs within their organisations.
Meeting Schedule:
09:00 – Registration & Welcome drinks
09:30 – Welcome & Introduction
09:45 – Industry Talks (x2)
10:45 – Refreshments & Exhibition
11:15 – Industry Talks (x2)
12:15 – Paul McIntyre Award Presentation
12:45 – Lunch & Networking
13:30 – Industry Talks (x2)
14:30 – Facility/Lab Tour
15:00 – CED Working Group Meetings
16:00 – Closing Discussions
16:15 – Finish
A recent article describes the effects of epoxy binder, curing agent, filler, initial solvent concentration, curing temperature, and relative humidity, on the curing-induced internal stress in epoxy coatings.
According to the report, curing-induced internal stresses in epoxy coatings are highly influenced by the type and concentration of their ingredients, and the conditions applied. In this new work, the effects on the internal stress development of the epoxy/crosslinker chemistry, curing temperature, relative humidity, filler conditions, and initial solvent concentration, were studied. An elevated curing temperature (35 or 45 °C) resulted in a smaller elastic modulus and, despite an accelerated curing reaction and a higher final reactant conversion, only a slight increase, around 0.2 MPa, in the average internal stress. An increased relative humidity (from 35 to 60 %), also resulted in a smaller elastic modulus and less volumetric shrinkage and internal stress. However, at 90 % relative humidity, the internal stress, due to an enhanced final reactant conversion, was higher than observed at 60 % RH.
The study noted that the presence of either BaSO4 or CaCO3 filler in the formulation reduced the final reactant conversion and volumetric shrinkage, but resulted in a higher elastic modulus and internal stress. 0.6 MPa.
The study presents guidelines to optimise coating formulations and curing conditions to avoid internal stress.
The study was published in Progress in Organic Coatings, Volume 173, December 2022.