The cart is empty!
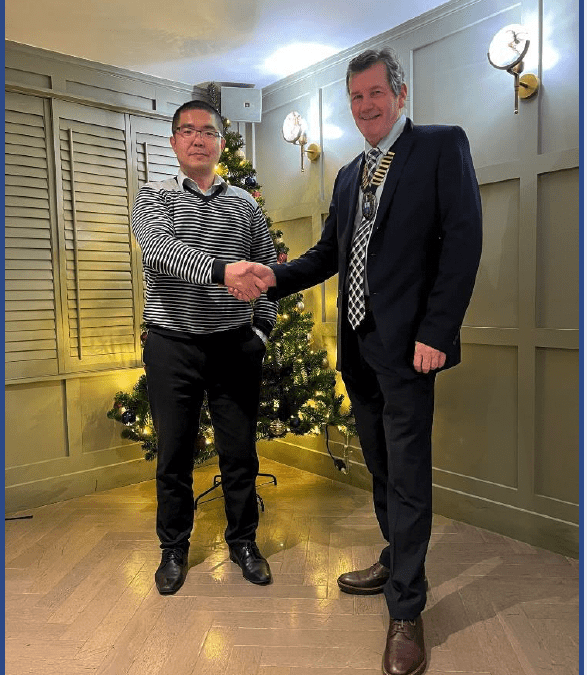
This series of articles is intended to highlight industry wide engineering experiences, practical opinions, guidance, and focused advice to practising technologists. The series is written by ICorr Fellows who have made significant contributions to the field of corrosion management. The articles in this issue feature contributions from David Harvey, who gives a personal view of his career as a senior CP Engineer, and Douglas Mills, who discusses the use of Electrochemical Noise Measurement in determining corrosion.
A Career as a Cathodic Protection Engineer
This article highlights some aspects of an interesting and rewarding career in the cathodic protection industry and with the Institute of Corrosion. It aims to show what can be experienced within the workplace and outside of it, in a varied, fascinating and satisfying career over 50 years gained with consultants, oil and gas operators, cathodic protection companies and engineering design houses. Hopefully this will encourage newcomers to the industry that there is great career to be had in cathodic protection.
I, like many others, came into cathodic protection by accident. I joined a CP Specialist Consulting Engineering Company as a draughtsman while still completing my day-release HNC in Electrical Engineering. I was fortunate to have an excellent mentor in David Lewis, former ICorr President, who gave me John Morgan’s “Cathodic Protection” textbook to study. I progressed on to become a CP design engineer. As I did not drive at that time and site visits were limited, I benefitted from picking the brains of my colleagues’ knowledge and site experience, as back then, junior engineers were teamed up with a senior engineer to learn their trade, which regrettably does not happen today. However, one of the enlightening aspects about the CP Industry is that senior engineers are generally very open in sharing their knowledge and experiences – both good and bad – to enable us to continually improve the way we approach projects and produce more cost effective, efficient designs.
CP Engineers come from many different disciplines (e.g. mechanical, electrical, chemical, civil etc) some from grass roots and others from universities. The application of CP to structures requires detailed interaction with all disciplines so one ends up knowing a little about a lot, rather than a lot about a little, unless specialising in one particular area. Rarely are two projects identical as there are so many different parameters to be considered. Today, there are training courses, exams and certification offered by ICorr at all levels from Tester to Senior Design Engineer (Levels 1- 4 of ISO 15257). However, CP is something you also need to learn from field experience – often by trial and error. It is not something you can just study and apply effectively from a desk alone. Design spreadsheets can often contain errors or have bad data inputted so the output needs strong experience to know if it is sound or “rubbish”.
My practical experience was initially gained by secondment to Middle Eastern oil companies. It covered applying cathodic protection to oil and gas fields, pipelines, associated tankage, and marine facilities. This was a very exciting time for a young man who had not previously been out of the UK. Working in the desert oil fields was almost like being on Safari. On return to UK, I was appointed a CP project engineer. Over time, I moved up to Engineering Manager and Consultant in a number of cathodic protection companies, design houses and as an independent consultant.
I was responsible for all aspects of sacrificial anode and major ICCP systems for pipelines, refineries/petrochemical facilities, and inshore/offshore marine structure projects.
My career as a cathodic protection engineer has given me the opportunity to visit and work in more than 25 different countries and meet many exceptional people at all levels. Occasionally, one could find sufficient spare time to visit some of the local tourist attractions, e.g. various roman ruins, Great Wall of China, Great Pyramids, Panama Canal etc. which were very enjoyable benefits I would not have otherwise gained.
ICorr Activities
As the industry expanded in the 1980’s, I became involved in ICorr activities when they had the Joint Venture with NACE (CCEJV), which became the Corrosion Engineering Association (CEA).
Initially, I joined a CCEJV cathodic protection work group to assist with the preparation of a State-of-the-Art Report to be published by ICorr and NACE. This enabled me to learn from my peers and, at the same time, put some of my experience back into the industry for the younger engineers to benefit from. Later, I became Work-Group Chair, then Task-Group Chair. I was then appointed Technical Activities Coordinating Committee (TACC) Chair. This role also included being the Conference Programme Manager for “UK Corrosion” which was a major three-day event in the corrosion world 1987-1991. As TACC Chair, I also attended NACE Committee Weeks and Corrosion Conferences in USA as the UK ICorr/CCEJV representative. This was a tremendous opportunity for interaction with cathodic protection engineers and manufacturers from around the world. Regrettably, after much good work, NACE and ICorr parted company in 1988 and the CEA became the Corrosion Engineering Division of ICorr.
I also became the representative for Pipeline Industries Guild and the Institute of Petroleum on the BSI CP GEL 603 committee in 1985 which was revising the UK CP bible, BS CP1021. This was eventually published as BS7361 in 1991. In 1993 I was elected to chair this committee, a post I held for the next 19 years, coordinating the UK input into numerous BS/CEN CP standards prepared and published during this time.
Apart from the BSI committee, I also became involved in various ICorr committees and Council:
• Member of Council 1998-Present.
• Chair of Professional Assessment Committee 1998 – 2012.
• Chair of CP Certification Sub-Committee 2006-2019.
• Chair of Course Approvals Board 2013-2019.
• Member of CP Governing Board (2002- 2020).
• Member PDTC Committee (1998-2020).
• QA Advisor attaining ISO 9001 Certification.
• ICorr Representative for UK to CEOCOR (2008 – 2012).
• Professional Affiliate Engineering Council Coordinator with Society of Operations Engineers – current role.
• Primary author/updater of 5 ICorr CP training Courses to ISO 15257 for On-land and Marine Structures.
As a result of these activities, I was awarded Honorary Fellow Member of ICorr in 2018.
One of the other milestones in my career was attaining Professional Affiliate Status for ICorr with the Engineering Council. This was followed by the setting up a Registration Agreement with the Society of Environment Engineers enabling suitably qualified and experienced members to apply for registration with the Engineering Council as a CEng, IEng or EngTech. Having set the system up, I thought I should be the guinea pig to try it out. My application was successful and I was awarded CEng. With the demise of SEE, I set up a new Registration Agreement with the Society of Operations Engineers.
As a result, more than 50 of our members have become registered as Chartered Engineers – a tremendous benefit available for our professional members.
In Conclusion
As I look back over the last 50+ years, I can reflect on the many good memories of a varied career, the many friends and colleagues I have worked with and the opportunities I was given to expand my knowledge. I have tried to put back some of this for young engineers to consider that a career in CP can be very interesting and rewarding. To be honest, I still get satisfaction from it and in retirement, I am still dabbling, doing some CP design appraisals/approvals. A long and interesting, satisfying career in CP is very achievable albeit with a lot of hard work.
David Harvey CEng, FICorr(Hon)
A Cathodic Protection Engineer at work.
Members often ask what the organisational structure of the Institute is, and to answer this, a series of articles has been planned, starting with an overview of the Institute’s structure.
The Institute of Corrosion is a not-for-profit organisation, dedicated to putting its members at the heart of the global corrosion prevention community and ensuring that all that is done is aligned to its core values:
• Trust and respect
• Experts and leaders in the field
• Innovative and forward-thinking
• Supportive and inclusive
The organisational structure is the framework that enables this, and in which many talented and hard-working corrosion professionals help us to achieve our goals. The Head Office, Corrosion House, is where all the admin work is conducted, and is located in Northampton, where the staff of three work tirelessly to ensure the smooth running of ICorr.
The Council of the Institute of Corrosion
The Council is like the Board of Directors of a large company. It is the Institute’s highest decision-making body, and every branch, division, and committee, reports to the Council, which is made up of the following members:
• The five trustees/directors
• Branch and division chairs
• Committee chairs
• The chair of Young ICorr
• The technical Editor of Corrosion Management magazine
• Various co-opted members
The Trustees of the Institute of Corrosion
There are five trustees, and these form the ‘committee’ that oversees the routine running of the Institute between Council meetings. The trustees are the following Institute members:
• The President
• The Vice President
• The Immediate Past President
• The Honorary Secretary
• The Honorary Treasurer
Beneath the Council, the structure allows information and operations to flow freely in all directions.
The Branches of the Institute of Corrosion
The six regional branches let us reach deep into the heart of the corrosion community in the UK:
• Aberdeen
• London
• Midlands
• Northeast
• Northwest
• Yorkshire
The work they do, and the networking opportunities they present to our members is vital. The branches have a great deal of autonomy, and run various events, including technical meetings/webinars, workshops, and social events.
Every event within the branches is a networking opportunity, and a chance for members to learn and share ideas, experience, and best practices.
The Two Divisions of the Institute of Corrosion
The two divisions stretch across every part of ICorr.
The Corrosion Engineering Division (CED)
The CED is made up of five working groups which look at specific aspects of our industry. The CED also runs an annual Working Day and Symposium. These Working Groups are:
• Nuclear Corrosion
• Coatings
• Cathodic Protection
• All Energy
• Corrosion in Concrete
The Corrosion Science Division (CSD)
This division consists of representatives from the corrosion research community – primarily academia and research – and runs the annual Corrosion Science Symposium.
Young ICorr
While the experience of senior corrosion professionals is crucial to our industry and to the Institute, equally important are the younger engineers and scientists who are entering and progressing in their careers in corrosion control.
Young ICorr is a vibrant and forward-looking group, through which many initiatives and early-career networks are formed, and from which the corrosion industry leaders of tomorrow will develop.
The Committees of the Institute of Corrosion
Finally, to the committees – without which the Institute could not function effectively. This is where much of the day-to-day work is managed. These teams meet when needed, collaborate with other teams, and ensure that actions agreed are carried out.
The Awards Committee
Responsible for overseeing the portfolio of ICorr awards, and for the nomination of members for external awards. The recognition of excellence both internally and externally helps us to demonstrate the authority with which the Institute operates and the professionalism, knowledge, and expertise of our members.
The Building Management Committee
This committee is responsible for the maintenance and upkeep of our Head Office, Corrosion House. They may not get their hands dirty with building work, but without them we might not have a home!
The Course Approval Board
The education of the corrosion community, at whatever stage of their individual careers, is crucial to the future of our industry, and, indeed, the future of our world. The Course Approval Board is responsible for approving new courses proposed by the Professional Development & Training Committee.
The Professional Development & Training Committee (PDTC)
PDTC is responsible for one of our most important strategies – the development and upgrade of training courses offered by the Institute. To achieve this, PDTC has two sub-committees:
• The Cathodic Protection Governing Board (CPGB), responsible for cathodic protection courses
• The Surface Treatment Governing Board (STGB), responsible for surface treatment courses
The Digital Strategy Committee
In our digital world, it is easier to connect, build networks, and share expertise than ever before. However, to do this effectively, it is essential to develop and follow a strategy that aligns with the goals of the Institute. This is the remit of the Digital Strategy Committee.
The Membership Development Committee
The real strength of the Institute lies in its membership. The broader and deeper our membership is, the more we can offer and provide to them and the global corrosion community.
The Membership Development Committee is responsible for initiatives to increase our membership and highlight the benefits for members.
The Professional Assessment Committee (PAC)
While the Membership Development Committee is responsible for driving up membership applications, it is the PAC that handles membership and upgrade applications.
Correx Limited
Although the Institute is a not-for-profit organisation, our commercial activities are key to the present and future sustainability. However, it is also crucial that the operation of these is kept at arm’s length to satisfy the requirements of the Charity Commission. To ensure this is the case, we registered Correx Limited in 2003 (the name was derived from “Corrosion” and “Exhibitions”). Correx organises all of our commercial activities, and especially the administration of ICATS (Industrial Coating Applicators Training Scheme), which is mandated by the Highways Agency and Network Rail for all coating applicators – and it is also a requirement for many other major structure owners including Oil Companies, Power Generators, and Infrastructure Owners.
It is intended to explore each element of the organisation structure of ICorr in more detail in future articles, to help our members and the wider corrosion community to have a greater understanding of all parts of the Institute and the tremendous amount of work that goes on behind the scenes. If you’re interested in getting involved in any of these activities, please get in touch with us.
The Journey described by Isaac Catran, Florentina Melo (ABRACO) and Lucia Fullalove (ICorr).
As ABRACO, the Brazilian Association of Corrosion, becomes nearer to getting ICATS, and the ICorr Paint Inspector Conversion course, we would like to take readers on the journey travelled so far.
It was in May 2018, during the INTERCORR (International Corrosion Congress) in São Paulo, Brazil, that ABRACO’s technical staff, Florentina (Flor) Melo and Isaac Catran met with Lucia Fullalove. Flor and Isaac were responsible for the training and qualification of corrosion professionals for ABRACO, and Lucia was in Brazil to deliver a ‘plenary talk’ on the “Application of Lean Principles in Corrosion Protection”, as a guest of INTERCORR.
As brief introduction, ABRACO is the Brazilian association which has represented the corrosion professionals in Brazil for over 50 years, it promotes and disseminates knowledge about corrosion and corrosion protection, and qualifies professionals in industrial paint application, industrial paint inspection, and cathodic protection. In addition to the above, ABRACO also delivers courses in the areas of pipeline protection and hot dip galvanising, for those professionals wanting to expand their knowledge.
Following the introductions, we (Lucia, Isaac and Flor) started to discuss the professional courses on corrosion protection from both our organisations, and we identified a great synergy between ourselves and the courses, and the possibility of closer co-operations between the organisations became our main target.
At ABRACO head office in Rio de Janeiro, the three of us made a presentation to the President of ABRACO at the time, Prof Laerce de Paula Nunes. The objective of the presentation was to propose a partnership which would allow for the promotion of ICorr in Brazil, as well as promoting ABRACO internationally. In addition, we wanted to get an agreement and recognition by ICorr for the paint inspectors trained and qualified in Brazil. Thus, providing the ABRACO paint inspectors with an internationally recognised qualification.
The collaboration project, “ICorr- ABRACO”, was immediately welcomed by the ABRACO President who under the advice of Lucia Fullalove, sent a message to the then President of ICorr, Sarah Vasey, introducing ABRACO and explaining the intention of creating a partnership between the two organisations. The positive response from ICorr was swift, and ‘we’ started to outline the co-operation project whilst still in May 2018.
Initially it appeared that the best way to progress would be with a direct comparison between the qualifications of both organisations in the areas of paint Inspection, paint application and cathodic protection. Therefore, a Memorandum of Understanding (MoU) between ABRACO and ICorr to show the intentions was created, the terms agreed, and finally signed by the then current Presidents of
the respective organisations in June 202,
Dr Olga Ferraz (ABRACO) and Dr Gareth Hinds (ICorr).
This partnership between ICorr and ABRACO was anticipated to go beyond the technical recognition, but also allow for further exposure and recognition of ICorr in Brazil where there is a huge potential for training development due to the country’s size, and the recognition by major players across several market sectors that corrosion protection is paramount, and of great benefit to asset owners.
On the other hand, ABRACO is well recognised in Brazil for the high standards of its qualification and quality of the training of corrosion professionals, therefore the partnership with ICorr will keep these high standards, and will give the Brazilian professionals the opportunity to also have international recognition.
As soon as the MoU was signed, we (Isaac, Flor and Lucia) started to work in earnest to focus on the equivalence for the certification of paint inspectors. From the very beginning the difference between the levels of qualifications was identified.
In Brazil, the paint inspectors’ certification is divided into 2 levels, whereas in the UK it is in 3 levels. Therefore, the first step was to see how the equivalence could be achieve, and the way forward was chosen to be to analyse and compare the course syllabuses. The idea was these would be assessed and a proposal made as to how this equivalence could be achieved, decided.
In March 2019, the contents of the ABRACO Paint Inspectors levels 1 and 2 courses were sent to be appraised and evaluated by ICorr. John Fletcher of ICorr was appointed to carry out this work, and in December 2019 following a GAP Analysis, he identified that the ABRACO Level 1 course content addressed most of the content of the ICorr Paint Inspectors levels 1 and 2, however there was a shortfall in the areas of H&S and the International Maritime Organisation ballast tank coating regulations. In the initial GAP Analysis, John also proposed options for the equivalence and a conversion module for this recognition has been proposed.
In March 2020, on the return to the UK, Lucia made a presentation to ICorr PDTC, which described the excitement and expectation created by the Brazilian paint inspectors for this ‘conversion’ from ABRACO to ICorr. Isaac, Flor and Lucia then carried out a mapping exercise between the Brazilian and the International Standards, so that ICorr could become acquainted with the Brazilian Standards and understand that the Brazilian paint inspector, although working under local standards, do have the level of work practice equivalent to their international counterparts.
The remaining differences were identified as relating to Brazilian legislation. Unlike in the UK, in Brazil, H&S activities on site are carried out by a Safety Medical professional, and by a Health & Safety qualified engineer. In addition, Brazilian technical standards are supported in law, therefore some of the activities of a corrosion protection professional must follow these. In Brazil, the standard even determines how the paint containers are stacked in storage.
The conversion module and exam questions have been written by Kevin Harold on behalf of ICorr, and the course translated, and reviewed. will be translated into Portuguese to be delivered in Brazil. The conversion course has now been uploaded to the IMechE Learning Management System. It is anticipated that once the Brazilian paint inspector takes the conversion module they will sit and online examination and the successful candidates will have their ABRACO L1 paint inspector certification, confirmed as an ICorr L2 paint inspector.
We would like to point out our certainty regarding the success of this project. This was one of the reasons Lucia was invited to deliver a presentation about the “ABRACO – ICorr” project at the Brazilian seminar of Anti- corrosive painting (SBPA) in Brazil in December 2019. The main attendees to the event were paint Inspectors and the project was well received by the audience.
The conversion module for L1 ABRACO Inspector was launched in Brazil on the 28th March, and the the next natural step is to get a similar process for the recognition of the L2 ABRACO paint inspectors as ICorr L3. Whilst a lot of training activities came to a halt as consequence of the COVID 19 pandemic, Isaac, Flor and Lucia started to work on the paint applicators course, and how to get the ICATS to Brazil.
ABRACO also wanted to have the ICATS in Brazil ‘online’ and Lucia has translated the modules and has been working with Isaac Catran to ensure the correct ‘ site jargon’ . as well as the Brazilian working practices are incorporated into the course. The translated ICATS modules have also been uploaded to the IMechE LMS system for ‘online’ access. This is now being tested , and although no definite date has been agreed for the launch, a trial is due to start soon.
As in the UK, in Brazil the training of paint applicators is carried out in parts. The ICorr Industrial Coating Applicator Scheme (ICATS) starts with a module on understanding the principles of corrosion protection, the importance of a good surface preparation before treatment, and the role of paint. And at this fudamental level the ICA is trained on the use of the paint brush and roller. It is ABRACO’s intention to follow thus training sequence. In 2020 this project was also introduced to Kevin Harold (MD of Correx) who was excited about the prospect, and proposed the setting up of the online Industrial Paint Applicators course (ICATS) in Portuguese to provide training to paint applicators in Brazil. The practical part of the course as well as the technical evaluation of the students (candidates) will be done by ABRACO.
The initial course (brush and roller) is currently being translated into Portuguese and the course contents adapted to the Brazilian legal requirements, environment, and work procedures.
For the practical assessment, Flor and Isaac had already developed a form to evaluate the students. which covers all the activities carried out by an industrial painter. This was shared with Kevin Harold to be assessed, and a modified version produced, which will be discussed and agreed by all (Kevin, Isaac and Lucia) as the new evaluation form for the ICATS Brazilian Industrial Paint Applicators.
In December 2020, there was another virtual SBPA (seminar on anticorrosion paints) meeting, which had 130 attendees, and at which Lucia was invited to, and delivered a presentation on the progress of the cooperation between ICorr and ABRACO. At this, there was great interest from both paint inspectors and paint applicators waiting to be able to take the ICATS conversion course.
The ICorr – ABRACO partnership is now being recognised and awaited by several sectors of the Brazilian Industry, such as Oil and Gas, steel producers, mining, petrochemicals, and others. There are still other areas for growth in Brazil where the strength of this partnership will be well received.
Above: Lucia, Isaac and Florentina