Institute News
Dear Members,
A very special welcome to our new Overseas Members and our new Student Members who recently joined us. Please let me know if there is anything at all l can assist with to improve your membership experience with ICorr.
Our student Bursaries Scheme with The University of Manchester is now approved and will commence this September.
We are also working hard behind the scenes to offer a wider range of Training Courses, and to expand our technical programmes for 2023-2024, and with that in mind, l must mention our newly launched Microbiologically Influenced Corrosion training course. You will find a poster for this in your magazine, please display it in your workplace for others to see. Thank you. Details of our Corrosion Under Insulation (CUI) course will also be announced shortly.
A lot more has happened since the last issue, in June our Northampton HQ hosted the Engineering Council Licence review for our Chartership Scheme, with a great result from that audit. Under the skilled eye of David Harvey, we expect to move forward with ICorr’s own CEng Direct Scheme in 2024.
Also at HQ, our Correx team is preparing to roll out the new ICATS Apprenticeship Scheme, with Kevin Harold working hard to launch it soon. The first two ICATS apprentices were tested
on July 12. https://www.icorr.org/correx/
Our NE Branch Sustainability Conference was a hugely successful event in Newcastle on June 22nd and 23rd, a true showcase for all that ICorr sets out to achieve in the fields of corrosion education and industrial partnerships. Very well done to all the NE committee members who have great plans going forward.
On June 28, the North-West Branch held their AGM and hosted an industrial visit to the Sherwin-Williams paint facility in Bolton. Interaction with the industry like this keeps everyone up-to-date and helps our branches thrive. A special thanks to Greg and all involved there.
On August 22, we will once again be offering our Corrosion Awareness Day in Aberdeen, which has proved very popular in previous years. See our events for August 2023 – Institute of Corrosion (icorr.org).
Finally, a reminder for our Corrosion Science Division’s 64th Corrosion Science Symposium (CSS) at the University of Bristol on September 10–12, 2023, including the UR Evans Award and Plenary Lecture. We do hope you can support that.
All our branches are becoming increasingly active in the U.K., and we hope to have some Overseas offerings soon too!
We very much look forward to you joining us soon, either in-person or online, for our 2023- 2024 ICorr Technical Sessions run by our UK branches.
Our ICorr calendar is regularly updated,
https://www.icorr.org/events/
I hope you will maximise the benefits of your membership by participating in these fantastic networking events.
Wishing you a great summer break.
Stephen Tate, President Institute of Corrosion

Institute of
Corrosion
President,
Stephen Tate
Ask the Expert
Question:
Why are coatings often supplemented with cathodic protection to protect against corrosion?
Answer:
Corrosion is one of the most critical failure mechanisms in structures, installations, components, and mechanical systems, in which materials go through decay or deterioration, which in turn compromises the integrity of these structures or systems. Deterioration is the cause of the formation of oxides, hydroxides, or sulphides, which are naturally more stable forms of any refined material. There are several reasons for corrosion to initiate and propagate, these include environmental and operational conditions, material properties, and electrochemical activation. Although several factors are involved in initiating and propagating corrosion, a key factor is the availability of an active metal surface, which incubates electrochemical changes leading to corrosion.
Therefore, the primary focus, as a cost effective, efficient, and reliable technique, is to convert the active metal surface areas into passive surface areas. This helps stop or decelerate corrosion, and can be done by providing a protective current, which in turn reduces the potential of a metal surface. This results in cathodic protection, hence stopping or significantly reducing electrochemical changes, in other words, any corrosive attack is halted. There are two conventional methods by which passivation of metal surfaces is achieved. These are commonly known as (i) sacrificial anode cathodic protection, and (ii) impressed current cathodic protection. The above methods have been widely used in several industrial applications, such as petrochemical, marine, and infrastructure. Another effective technique for mitigating corrosion is to use a coating. The coating acts as an anti-corrosive protective layer, a barrier, or a sacrificial layer over the metal. Coatings offer several benefits by protecting materials, enhancing surface characteristics, and avoiding or reducing the risks of failure. Corrosion, however, becomes more complex in terms of its failure mechanisms when structures and components are dynamically loaded as in marine structures. This will cause failures such as corrosion fatigue and stress corrosion cracking.
Or when static structures are exposed to more aggressive environments, corrosion and corrosion failures will significantly accelerate. The combination of both coatings and cathodic protection will enhance metal resistance against corrosion. Therefore, a combination of both is widely used. These preventative methods also assist at the design stage in reducing the required weight of material for required operating lifetime and can thus significantly reduce fabrication and later transport costs with net-zero type benefits.
A more complex corrosion mechanism will occur when components are dynamically loaded and are subject to relative motion. This adds more complexity to attempts at stopping or controlling corrosion, because other mechanical and physical factors are now combined and are contributing to a more complex form of deterioration. In such instances, the use or application of cathodic protection becomes complicated, challenging, and in some cases, it becomes almost impossible to meet specified CP criteria. Therefore, more robust methods of enhancing corrosion resistance through material development, advanced coatings and coating techniques, corrosion monitoring, and prognostic measures, have been developed over the past several years. It is more pragmatic to provide bespoke solutions for specific applications.
If the components are interacting, then surface wear will occur. In a scenario where corrosion is absent, the wear purely results from mechanical loading and surface deterioration. However, in the presence of corrosive species, corrosion will also occur. This leads to a wear-corrosion mechanism.
Recent Coating Developments
Researchers have been developing advanced coatings to withstand both corrosion and wear in challenging and harsh environmental and operational conditions subject to design life requirements. Recent developments in nanocoatings and nanocomposite coatings [5], have shown that more attractive coating solutions are available for applications in more complex mechanical and chemical conditions. These nanocomposite coatings are, for example, Ni/Al2O3, Ni/SiC, Ni/ZrO2, Ni/Graphene (GPL), and several others. Such coatings have been developed in order to be subjected to corrosion while incorporating the effects of key mechanical properties. These newly developed nanocomposite coatings have been tested according to ASTM B117,
salt spray testing [1].
Further study of the above nanocomposite coatings has been conducted within the wear context [2].
A comprehensive study of the above nanocoatings at atomic surface layers, incorporating corrosive fluids, and using a numerical approach, was conducted [3].
It is well known that the durability and reliability of complex interacting systems are very important from a cost viewpoint and within a wider sustainability context. These interacting systems are subject to corrosion failures and are therefore a major concern for industry professionals. It is important to fully diversify design parameters.
Remote Monitoring
Further work has been performed to predict corrosion in dynamically corrosive environments by considering physical and mechanical characteristics. Researchers have recently developed and patented a new corrosion sensor that could improve the safety and reliability of large structures such as bridges, aircraft, military vehicles, and gas pipelines. The device can detect defects and risks in major infrastructure at a much earlier stage than the methods that are currently used. As well as improving safety, it could reduce the need for time consuming repairs, which can come at a significant cost and inconvenience to industries and the public.
In summary, it evident that the primary objective of an industrial coating is to prevent corrosion, and to withstand a variety of hazardous chemicals. Choosing the right coating is just as important as choosing the coating itself, a wrongly specified coating can lead to a wide range of problems, from maintenance to premature failure. No coating is completely free of defects, even when freshly applied. Faults can occur during the production of the coating as well as during handling and improper application of the coating. A defect may also arise during the course of service. The most common causes of coating failures include inadequate surface preparation, a non-friendly environment, poor formulation, and an inefficient application technique. Coatings with high efficiency are more expensive. Thicker coatings, the use of sophisticated inspection methods, and fixing specific defects, all result in higher cost and critically weight. Sometimes it is advantageous to use another protection method to supplement coatings, which is why we use cathodic protection and especially in marine situations. There is an overall benefit when a good coating application is combined with cathodic protection [4].
Prof. Zulfiqar Khan, Bournemouth University NanoCorr, Energy & Modelling (NCEM) Research Group.
References
1. Nazir, M.H., Khan, Z.A., Saeed, A., Bakolas, V., Braun, W., Bajwa, R. and Rafique, S., 2017. Analyzing and modelling the corrosion behavior of Ni/Al2O3, Ni/SiC, Ni/ZrO2 and Ni/graphene nanocomposite coatings. Materials, 10 (11).
2. Nazir, M.H., Khan, Z.A., Saeed, A., Bakolas, V., Braun, W. and Bajwa, R., 2018. Experimental analysis and modelling for reciprocating wear behaviour of nanocomposite coatings. Wear, 416-417, 89-102.
3. Nazir, M.H., Khan, Z.A., Saeed, A., Siddaiah, A. and Menezes, P.L., 2018. Synergistic wear-corrosion analysis and modelling of nanocomposite coatings. Tribology International, 121, 30-44.
4. L.L. Sheir, R.A. Jarman, and G.T. Burstein; “Corrosion”, Volume 2: “Corrosion Control”, 3rd edition, Butterworth Heinemann, ISBN 0-7506-1077-8.
5. https://www.digitaljournal.com/pr/news/theexpresswire/nano-coating-market-by-2031
Continuity Straps across Flanges for providing Cathodic Protection.
Institute News
Each year, the Institute of Corrosion bestows a range of internationally renowned awards in recognition of excellence in corrosion science and engineering, and to reward outstanding service to the Institute and the wider corrosion community.
The institute is extremely proud to announce the selection of Trevor Osborne, FICorr (Hon), NACE Corrosion Specialist, for the H.G. Cole Award.
This award is made in recognition of exceptional services to the development of the Institute. It is only awarded on an occasional basis, reflecting the highest possible level of commitment of the recipient to the activities of the Institute. The inaugural H.G. Cole Award (in the form of a poignard) was presented to Charles Booker in 1997 by Gwen Cole (wife of the late Henry Cole), in recognition of his many years of service as Honorary Secretary of the Institute. The modern form of the award is a plaque whose design captures the essence of the original poignard.
Trevor is a past president of the Institute of Corrosion and a long-standing chair of the board of its commercial arm, Correx Ltd. He is managing director of Deepwater Corrosion Services (UK) Ltd., and has worked in the energy industry for over 43 years, with very wide experience in corrosion control and project execution. He will be presented with the award at the Institute AGM to be held on November 8, 2023, in Birmingham.
We offer our sincere congratulations to Trevor on this magnificent achievement.
Background to the H.G. Cole Award
Henry George Cole was the chief materials engineer at the UK Ministry of Defence. He was based in London and Farnborough, and was a hugely respected coordinator and sponsor of research, an elegant and influential ‘Whitehall Mandarin’, and a man of spectacular vision and determination. He was Secretary to the Hoar Committee, a ground-breaking development for the recognition of corrosion costs in the early 1970s that was the mainspring for corrosion interest in UK government circles for the next twenty years. Henry Cole was also hugely committed to the Institute of Corrosion. He became the part-time administrative officer for the institute when it shared accommodation with the SCI at Belgrave Square. He oversaw the Institute’s move to the IMF offices in Birmingham and he was one of the guiding lights of the Institute until his untimely death on 14th May 1987.
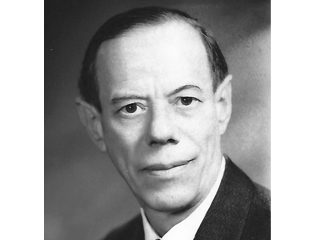
Trevor’s Legacy
Trevor has made an outstanding contribution to the long-term financial sustainability of the institute in a variety of roles over many years. He has guided the Institute financially by overseeing the continued success of our ICATS training scheme in his role as Chair of the Correx Board, and by coordinating sound investments on our behalf. In addition, before retiring from Council in 2022, Trevor spearheaded the purchase and refurbishment of a new headquarters for the Institute – ‘Corrosion House’ in Northampton.
This is a ‘state of the art’ 3-storey building, with the ground floor dedicated to the HQ administration team, the middle floor for training, and the top floor as a conference room. Each floor has its own kitchen, and the corrosion training centre has a breakout facility for delegates.
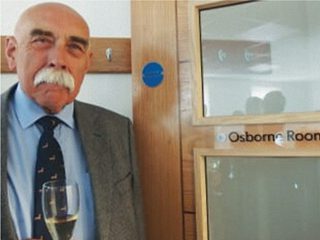
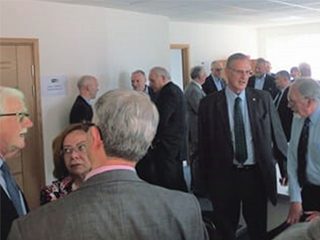
Corrosion House is undoubtedly a world class facility, totally fitting for the Institute of Corrosion, and based in a location in easy reach for both national and global customers, that today welcomes customers and members from all over the world.
More information on the H.G. Cole Award can be found on the Awards page of the ICorr Website:
https://www.icorr.org/icorr-awards/