Institute News
CED Day: The annual CED Working Day and Symposium, this year entitled ‘Corrosion Prevention in the 21st Century’, was held on Thursday, April 27, 2023, at the National Physical Laboratory (NPL), Teddington.
The day highlighted the need to share and transfer knowledge across all industries facing similar corrosion challenges. There were seven main talks and three working groups, led by Douglas Mills (coatings), Nick Smart (nuclear), and Steve Paterson (All Energy Group). This one-day meeting was the latest in a series of working days for the Institute of Corrosion’s Corrosion Engineering Division. Dr. Danny Burkle (Corrosion Testing Specialist – LBBC, Baskerville), Chair of CED, welcomed delegates to the meeting and introduced the speakers. He emphasised that the financial loss due to corrosion in the UK is 3.4% of GDP, or £77.5 M (comparable with defence at 2% or education at 4%). Danny thanked Nick Smart, the previous chair of CED, for his invaluable services over the past 15 years, and he presented him with a special award. Their shared vision is to bridge the gap between the CED and CSD divisions in future, to the benefit of both.
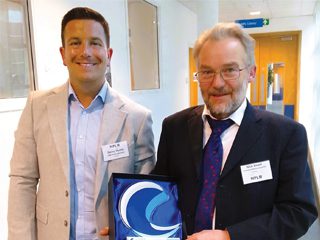
There then followed, ‘An introduction to NPL and NPL Activities’ by Gareth Hinds (Fellow and Science Area Leader, Electrochemistry Group at NPL), a past President of ICorr (2018–2020), the current President of the World Corrosion Organization (WCO), and Vice-President of the European Federation of Corrosion (EFC). Gareth outlined the history of NPL, founded in 1900, and active in corrosion research since 1924 (Guy Bengough (FRS) was an early scientist working there). Subsequently, Alan Turnbull, FRS, FREng, OBE, with 50 years of service at NPL, was introduced and applauded. The focus of government funded research at NPL is: net zero, offshore wind, nuclear waste disposal, and materials selection for these areas. Knowledge transfer includes: NPL corrosion guides, international standards, and industrial guidelines. NPL though continues to do a large amount of corrosion testing on behalf of oil and gas operators (separately, on a commercial basis).
Professor Alison Davenport (University of Birmingham) addressed the subject of “understanding localised corrosion’ and how this can improve corrosion prevention methods. The corrosion of metals in natural environments is a non-uniform process. Using synchrotron X-rays, water and metals are both penetrated, thus permitting mechanisms of formation and breakdown of passive films to be elucidated. A video study providing 3-D tomograms was shown. Rotating disc electrodes enable the growth of passive films to be followed via current transients over millisecond periods. These studies were necessary to assess the risk of fatigue failure in ageing aircraft, e.g., by atmospheric corrosion studies of NaCl deposits on Al-Cu-Mg alloys (AA2024). Similar methods were used to study the corrosion of stainless-steel containers used to store intermediate-level waste. The role of salt films in growing pits was described, along with their relationship to Pourbaix diagrams. At each point in a growing pit, it can be shown that the corrosion current is a function of metal ion concentration and the electric field through the droplet.
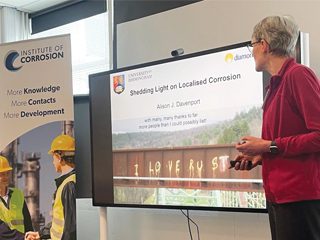
Dr. James Hesketh, (Principal Corrosion Science Consultant at Jacobs) spoke on ‘The corrosion of canisters during interim and deep geological disposal of radioactive waste’. There are three levels of radioactive waste: high, intermediate, and low (HLW, ILW, and LLW). Containers for LLW and ILW include unshielded, thin-walled stainless steel, concrete fabrications, and robust cast iron canisters, which have greater impact and fire-damage resistance. Intermediate storage items have been subjected to atmospheric corrosion over several decades. Key environmental parameters are % RH, surface chloride concentration, and time of wetness. Future deep geological disposal will provide permanent, safe disposal. One specification is KBS-3. However, a Swiss concept enabled progress to a more advanced stage. All present designs make use of a multi-barrier approach, comprising copper/carbon steel, with predicted lifetimes >10,000 yr. Despite the complexity and time-variation of corrosive environments, two distinct phases may be identified – early, ‘oxidic’ and long-term, ‘anoxic’. In-situ experiments involving boreholes were then outlined.
Alyshia Keogh (University of Manchester – PhD student) discussed her current research, on the ‘Effect of microstructure on localised corrosion and atmospheric stress corrosion cracking of 15-5PH stainless steel’. The type of microstructure influenced the susceptibility and was very dependent on the ageing temperature, 450 °C, 540 °C or 650 °C. Microstructural characterisation was carried out by STEM/EDX, and differences in pitting behaviour were assessed using double loop electrochemical potentiokinetic reactivation (DL-EPR), which found a linear trend in degree of sensitisation with ageing temperature, and which correlated with the increase in the presence of Cr carbides. Electrochemical noise measured by galvanically coupling dissimilar microstructures suggested that the higher temperature ageing treatment produced the most metastable pitting events. This may have a higher probability of transitioning to stable pitting. Four-point bend specimens with Cl- salt deposits exposed to controlled temperature and humidity revealed that higher ageing temperatures were more resistant to cracking. The mode of cracking changed from intergranular at 450 °C to mixed-intergranular and transgranular, at 540 °C, whereas no cracks occurred in samples aged at 650 °C.
After an excellent lunch there followed several further talks, including one by Roger Francis himself, together with a presentation of the Paul McIntyre Award to him, a very worthy winner. This award is among ICorr’s premier awards, and is presented to a senior corrosion engineer, who, as well as being a leading practitioner in their field, has advanced European collaboration and international standards development.
Roger has been a corrosion engineer for over 45 years, working in the fields of marine corrosion, desalination, sour oil and gas corrosion, mineral processing, and the chemical and process industries. He has published over 100 technical papers in all these areas, written six books on various aspects of corrosion, and jointly edited three others.
Dr. Steve Paterson, (Materials and Corrosion Adviser, Arbeadie Consultants Ltd.) then presented on ‘Applying materials experience from oil and gas production to carbon capture and storage’. Carbon Capture and Storage (CCS) processes prove challenging in so far as the CO2 source may contain impurities, and processing is determined by the level and type of these. Problems encountered in transporting the fluid include liquid dropout, corrosion, and running ductile fracture. Joule-Thomson cooling causes low temperatures with an attendant lack of toughness, the preferred option is to avoid drop-out. Essentially, it is important to consider transients/unstable conditions when assessing processes and defining CO2 specification limits. Also discussed were low temperature brittle fracture and hydrogen-related cracking mechanisms, Stress Corrosion Cracking (SCC), the use of corrosion-resistant alloys, the application of downhole barrier valves, and non-metallic materials.
Dr. Jonathan Mann (Nuclear structural integrity engineer, Jacobs) gave an entertaining but most important talk entitled ‘How to make trends and influence people’ which focused on how fatigue damage is increased by corrosive environments, and is a key consideration in numerous industries, including nuclear. Fatigue crack growth (FCG) studies had been initiated by Rolls-Royce and supported by Jacobs. Current predictive methods are fairly simple, providing over-conservative results. An improvement was to move to a better model, that reflected real behaviour. The ASME Environmental Fatigue document provides fatigue and FCG data for austenitic stainless steels in PWR water (low dissolved oxygen), and an equation relating fatigue life to temperature, strain rate, and oxygen concentration was given. Other factors affecting fatigue life include, varying amplitude, load, multi-axial loading, surface finish, material variability, non-isothermal loading, and thermal gradients. Consequently, rigs have been designed to investigate any type of waveform over a wide-range of temperatures.
Dr. Roger Francis, (Director at RF Materials) gave a resume of ‘The limits of copper alloy and stainless-steel heat-exchanger tubes’. Common alloys used for heat exchangers are, copper alloys (w/o), Al-brass, 90Cu/10Ni, 70Cu/30Ni, and 66/30/2/2 Cu-Ni-Fe-Mn, plus stainless steels, 304L, 316L, 20Cr/18Ni/6Mo; 2304 and 2205 duplex plates, Z100 and 2507 super-duplex. Erosion-corrosion and pitting/crevice corrosion are encountered.
With Al-brass erosion ’horse-shoe going upstream’ defects occur at velocities of 1.5 – 2.0 ms-1. Where seawater contains chlorine to prevent fouling, minimal concentrations should be used. If silt is present, corrosion rates rise rapidly with silt content. However, titanium shows no erosion-corrosion over the entire range of silt levels. For copper alloys, crevice corrosion is not a significant problem, and pitting corrosion is not problematic in fresh water. Sulphide ions at 0.1 mg/l cause pitting corrosion but may be mitigated by acid-cleaning. Super-duplex steels have demonstrated excellent corrosion-resistance since the early 1990s.
Dr. Anthony Setiadi (Chief Consultant / Associate Director – Wood Thilsted) presented finally on the ‘Benefits of using corrosion protection for offshore wind’. Monopiles (MPs) widely used in the supply of renewable energy presently range from 8–10 m diameter and 90 m high. However, for future MP’s, 15 m diameter and 120 m high are envisaged. MPs operate in 15 – 60 m water depth, deeper waters require jackets or floating foundations. In any case, increasingly large surface areas are involved. Corrosion protection via materials selection, corrosion allowances, coatings, and CP for sea-water immersed areas, were discussed. Coatings and cathodic protection support a large decrease in the tonnage of steel required for these structures. Percentage steel tonnages were compared to a ‘base cost’ and tables were presented for 25, 30 and 35-year timescales for C1, C2, C3, and C4 environments.
Typical losses (kg y-1 m-2) ranged from 1.56 in C5 to 0.624 in C4 environments. It should be noted that the coating type can impact corrosion protection very significantly as does control of application at build. Finally, the need to consider the different climates encountered was discussed: tropical, sub-tropical, temperate and arctic.
It was possible later in the day for participants to visit the extensive corrosion laboratories of NPL.
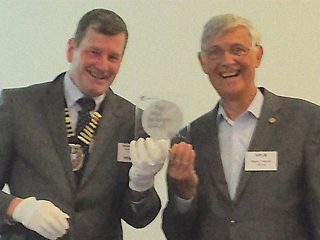
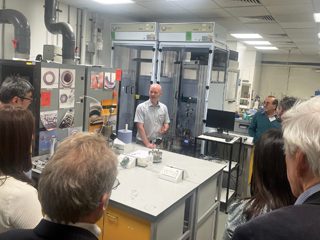
All CED presentations will be uploaded to the ICorr website for members to view and download. The three working groups will continue to advance their activities and will announce dates for further meetings in due course. To find out about next year’s CED event, or if you are interested in attending, speaking, or exhibiting, contact Dr. Danny Burkle, at danny.burkle@lbbcbaskerville.co.uk The CED is actively recruiting for a vice chair to assist Danny with growing the division. If this is of interest to you or a colleague, please contact Danny and let him know. Corrosion Management is most grateful to Dr David Nuttall, FICorr and Dr Douglas Mills, FICorr, for providing this event write-up.
Presentation to retiring CED Chair Nick Smart, By Dr Danny Burkle, New CED Chair.
Professor Alison Davenport (University of Birmingham) addressed the subject of ‘understanding localised corrosion’.
Presentation of the Paul McIntyre Award to Dr Roger Francis by Stephen Tate, ICorr President.
Dr Gareth Hinds – Fellow and Science Area Leader, Electrochemistry Group conducts a tour of NPL facilities with ICorr guests.
Blogs
“An Award for All in Corrosion” The CBE (Commander of the British Empire) is one of the highest awards the Monarch can bestow on an individual. King Charles presented his first New Year Honours in January 2023, and among the recipients of the CBE was Dr Liane Smith....
Institute News
On Thursday 19th January 2023, the EI Highlands and Islands hosted its annual Joint technical event with the branch, and welcomed Roland Anderson, Axess Corrosion Inc. who gave a talk on ‘Internal Corrosion Monitoring Systems – Enhanced Safety through Innovation’ with a specific focus on operational aspects. Roland has had over 20 years’ experience in the Oil & Gas industry focused on internal corrosion monitoring programmes around the globe, and has established businesses, in many locations including the UK, Middle East, Australia, China, and the USA. Recent years have been primarily focused on product innovation aimed at improving safety.
Mechanical retrieval tool designs for online corrosion monitoring servicing have been largely unchanged in 70+ years, the last major update to tooling being in 1978. Over 300 new ‘heavy duty’ retrievers are introduced into the field each year, and mechanical access fitting design has not changed since the first field installation in 1950.
Over 3000 new access fittings are commissioned each year and it is estimated that over 100,000 are in active service and many others plugged and decommissioned. High pressure retrieval tools and portable isolations are required for device changeouts under pressure (online). Incidents reported with this technology (although very rare relative to number of service operations) range globally from loss of containment, severe injury, and fatalities.
Several incidents over the last 25 years (mainly through incorrect training) had resulted in suspension of online retrievals especially in the North Sea.
An overseas fatality in May 2012 led to many other operators suspending online retrieval of intrusive devices. The fatality occurred during the retrieval of an ER probe installed at the 6 o’clock position on a slug catcher line. The access fitting had not been serviced in over four years. Scaffolding had been built to accommodate a technician, located directly below the retriever to help support the weight.
Life extension of assets, dilution of field experience, (through retirals and people leaving for other cleaner industries) and growing concerns around intrusive monitoring techniques, called for innovation to solve several problems.
Axess Corrosion responded to the new challenges by releasing the Janus™ Safety Guard, having consulted with Shell on the design, and piloted it successfully after the incident. The ‘Janus Guard’ removes the line of fire. It is retrofittable, auto deploying and built into the retrievers, replacing original components. The Janus Range provides retrofittable guards for telescoping and non-telescoping retrievers. Axess retrieval tools, with the guard attached, have been made lighter overall compared to other older devices without the guard. They are low cost, low maintenance and do not require re-certification
of technicians.
Janus Access fittings can be safer, and until now double isolation valves depended on a single O-ring between process and environment, however the Janus fittings incorporate two additional sealing faces, ensuring double isolation valves have double seals and the external threads are protected from the environment. Existing service valves can be adapted to realise these benefits at low cost.
Janus Type fittings have the following key advantages:
• Functionality applies to both mechanical and hydraulic system options.
• Janus is presently the only access fitting with a double seal and double isolation between process and environment.
• The radial sealing surface provides an additional seal for the service valve and the pressure retaining cover. This serves to seal the external threads from the environment with the O-ring carefully positioned on the access fitting.
In April 2022, Shell successfully completed a retrieval with the Janus™ tool, where retrieval of strip coupons installed at the high debris risk six o’clock position on a slug catcher line was completed. The access fitting had not been serviced in over four years due to the LFI, (learnings from incident) and subsequent Risk Assessment. The location was identified as a valuable data point for the integrity programme at QGTL (Qatar – Gas to Liquids) and the similarity to the LFI location was obvious. Other client projects are also reported to have received benefits, for example, ConocoPhillips now use the Janus modified retrieval tool on over 70% of its (CM) retrievals in Alaska, and over 2000 successful (CM) retrievals were conducted throughout 2022, with service technicians now feeling protected and secure. Optimised stroke lengths have reduced the overall weight of tools, and engagement of the service team has resulted in further tool enhancements and revisions.
Modified Janus™ Range offering:
• Applies to legacy tools to make them safer.
• Janus™ Safety Guard * – Finalist for 2023 AMPP Innovation Awards – 2023 Finalists (webflow.io)
• Minimal changes to existing (CM) retrievals procedures
• The outcomes of risk assessment studies conducted by energy operators have changed dramatically with new tool modifications deemed positive.
*Patents pending through USPTO (United States Patent and Trademark Office) and Patent Cooperation Treaty (PCT) protected.
An online ‘Plug & Abandon’ solution for redundant access fittings is available now along with devices for repurposing fittings for alternative uses, such as chemical injection. Conversion of access fittings to chemical injection points allows them to be serviced under pressure and are a low-cost piping modification. Additionally, there is no bulky flanged side tee, or troublesome NPT side connections, and the chemicals are isolated from access fitting material.
This company has also developed an improved Double Seal / Double Isolation device for use with a Janus type Access ‘intrusive’ fitting.
On Tuesday 28th February 2023, the branch meeting welcomed Raza Amin of Ankaa Consulting (Kuala Lumpur) and previously of GL Noble Denton, who gave a talk entitled ‘Enterprise Digital Solution for Asset Integrity Management’.
Mr. Amin has had 29 years of experience in engineering, technical consulting and advisory, training, and management. He has been responsible for leading safety and process engineering projects for the offshore oil and gas platforms and Mobile Offshore Drilling Units (MODUs), onshore gas processing plants, chemical plants, and refineries. He has worked on oil and gas facilities throughout Europe, Middle East, Africa, the Far East, and the Indian sub-continent.
Currently, he is Managing Director of Ankaa Consulting, concurrently taking the role as Asset Integrity Director and Process Safety Advisor. He manages projects in various disciplines, such as Integrity Operating Windows (IOW), Life Extension Studies (LES) for Offshore Assets, Risk Based Inspection (RBI) Assessments for Static Equipment, Piping, Pressure Relief Devices, Structures and Subsea Pipelines & Risers, Reliability Centred Maintenance (RCM), Instrument Safety Integrity Level (SIL), Engineering Critical Assessment (ECA), and also oversees the implementation of Alpha-Phe, a modern and comprehensive cloud-based database application module for the entire Asset Integrity Management System of Petrochemical industries.
Raza emphasised that while everyone is aware that we are in the digital age, the ambitions of a company and the means at its disposal to fully practice digital solutions are still often insufficient and / or inadequate. When controlled appropriately, data can yield the insights that make it more valuable than ‘black gold. Databases contain millions of records extracted through the various system interfaces used by operating companies that can enable understanding of complex relationships between many variables interactively.
Raza made clear that in today’s fast changing business landscape and aging assets, any Asset Integrity Management (AIM) digital solution needs to have an inherent capability to adopt to these changes – so a flexible system configuration approach is a necessary requirement rather than a nice-to-have.
• The system needs custom-built software which is ‘best in class’ having a single corporate system for all upstream and downstream assets, providing common understanding across all businesses.
• The software system must be’ holistic in approach using next generation technology, so it significantly reduces the cost associated with maintaining fragmented systems.
• It needs a complete system with AIM solution for every asset class and associated equipment, which is built on the latest codes, standards, industry guidelines and best practices, including ISO 55000.
He argued that with such a system in place it would be possible to improve work processes to achieve optimum work efficiency, communication between departments, and improve efficiency by eliminating duplication of work.
In the need for Digital Asset Integrity, Raza identified the fundamental problem in industry is that we have created too many data silos over years. We have seen so many different software systems and spreadsheets for AIMS, PIMS, SIMS, IOW, FFS, IDMS, and ANOMALIES. The key concern was that engineers presently manually fetch information from each system to make decisions and visualise overall health of an asset.
The need for a Digital AIMS to cover ‘day to day’ operations was put down to having improper workflow, leading to poor accountability. The various ‘day to day’ problems encountered without a system-based workflow can lead to following:
• No accountability.
• No audit trail.
• Unable to identify bottlenecks in the process.
• Unaware of the constraints – not seeing who missed out on an action.
And suggested solutions included:
• Generate time-based audit trails.
• Implement integrated workflow for each data points with seamless integration.
• Inform responsible party for action through notification.
• Utilise technology to manage accountability.
Digital AIMS avoids duplication of data / process / efforts.
Other issues identified:
• Difficulty in inspection planning that is time consuming leading to too many overdue actions.
• Multiple contractors managing various Integrity, inspection and reporting activities for different asset types with inconsistency in reporting.
• Same process done in different systems, hard to maintain multiple systems to improve processes.
Other suggested solutions:
• Require a common platform for work packs.
• Need to improve the interface between different parties by centralising and sharing information.
• Inspection reporting is required directly into the Data platform. Need to reduce data entry errors, perform QA/QC.
Razo concluded, that the presented integration platform helps interfacing the AIM system with the existing corporate systems and operational data systems to achieve continuous update of AIMS models, helps operators with up-to-date health status of the assets in the form of KPIs, and operators can then take timely key decisions on asset integrity. This type of system can be accessed from anywhere and at any time, which is powerful, robust, and fast module development platform. It meets all the modern features and functionality that is needed to measure the technical integrity of oil and gas facilities smoothly. With such a solution, i.e. a dedicated system that meets the overall company AIM requirements, and that covers the entire Asset Integrity work process and all disciplines. Analytics specific to each discipline then becomes possible and meaningful.
This presentation cleverly highlighted the holistic approach to managing Asset Integrity Management data, and raised many interesting questions from attendees in the Q&A session that followed afterwards.
Two former branch members are now thriving in the Middle East, Hooman Takhtechian has recently started a new position as Lead Corrosion Engineer at Bureau Veritas Group in Abu Dhabi, and Amir Attarchi who is now based in Qatar, and working as Senior Principal Metallurgy Engineer on NOC Ruya FEED project.
Presently there are 3 vacancies on the ICorr Aberdeen committee, for which invitations are invited to pursue officer roles. All enquires please to the branch chair, itsejaz@yahoo.com.
The branch has a very busy programme ahead and is pleased to announce the following upcoming events, for which registration details will be sent to all ICorr members nearer to event time:
On 25th April 2023, the branch has scheduled its 1-day Marine Corrosion Forum conference, a joint ICorr Aberdeen / Marine Corrosion Forum event. There is also an industrial visit to ICR in the evening. Places are limited for this event.
In May 2023, the scheduled events are, the joint ICorr / MCF CUI webinar week, Monday 15th to Friday 19th May [Lunch time events,12:00-13:00 each day], and a joint ICorr / AMPP technical session on Friday 19th May (evening), with a presentation by David Wickam and Chris Fyfe of AkzoNobel entitled: “Maintenance and Repair Solutions for Damaged or Aged PFP”.
Further Information about the branch, and past presentations, can be found on the website page: Aberdeen Branch – Institute of Corrosion (icorr.org), and to join the branch mailing list, please contact: icorrabz@gmail.com
Abstracts of potential papers for the branch technical programme are always welcome, and anyone wishing to present should prepare an abstract and correspond soonest with the branch Vice Chair – Adesiji Anjorin, anjorin@gmail.com, who is preparing the 2023/2024 events schedule.
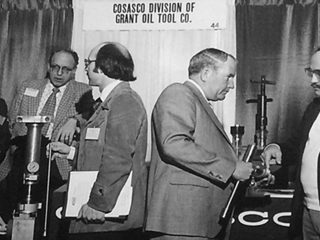
Initial launch of online corrosion monitoring (CM) retrieval tools.
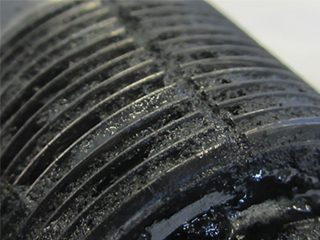
Example of thread debris – blocked pressure equalisation channel.
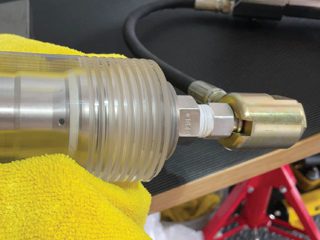
Fitting abandonment filling (by HP injection process).
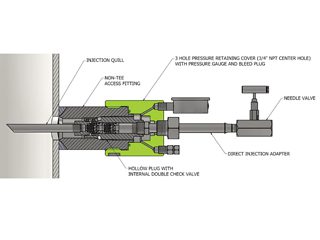
Fitting conversion to chemical injection point.
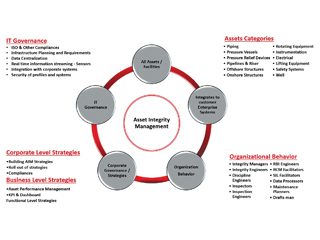
Holistic Approach to Asset Management.
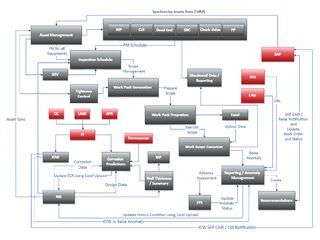
Work Elements of Asset Management.
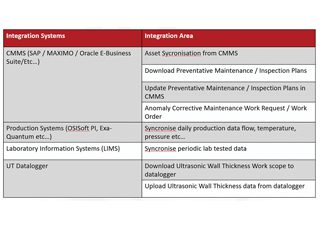
Integration Areas of Asset Management.
Institute News
The Division has announced with great pleasure that the next recipient of the UR Evans award, which will be presented at the 64th Corrosion Science Symposium (CSS), will be Prof Nick Birbilis.
Prof Birbilis has been a champion of corrosion education throughout his career with seminal contributions in many areas related to the discipline. He is currently the Executive Dean of the Faculty of Science, Engineering and Built Environment, at Deakin University in Victoria, Australia. Previously he was the Head of the Department of Materials Science and Engineering and the Woodside Innovation Chair at Monash University. His research interests include the broad areas of corrosion and corrosion control. His current focus is centred on microstructure-corrosion relationships, exploring the metallurgical factors that dictate localised corrosion initiation and propagation.
He graduated with a Bachelor of Engineering in 2001, and a PhD in 2004 (both from Monash). He was a postdoctoral researcher at Ohio State University before joining the Monash University staff. More broadly, he has worked on materials characterisation, and the use of advanced manufacturing for the development of more sustainable and durable materials, including bio-inspired and hybrid materials. He has been Associate Editor of Electrochimica Acta since 2010, and has been active in several societies, including the ISE, ECS and NACE. Nick has received several awards and presented numerous invited lectures. He is a Fellow of the Electrochemical Society and a Fellow of NACE. In 2016, Nick was awarded the ‘Woodside Innovation Chair’ at Monash, an industrially funded personal chair associated with durability of next generation materials.
The 64th CSS will once again join the Electrochem2023 meeting at the University of Bristol, on 11th and 12th September 2023.
Institute News
Welcome to the 2nd issue of our Magazine for 2023. A new editor has now been appointed, Dr Shagufta Khan FICorr, and to give her time to settle into the role, Brian Goldie, the outgoing editor, has very kindly agreed to stay in position for this issue. The May/June issue will be Shagufta’s first as editor, and Brian will assist her for the first two issues. Thank you to Brian for so much hard work and many congratulations to Shagufta, who may be contacted at: editor@icorr.org, if you have any news or technical articles to submit.
It has been a busy year so far, with a number of events having taken place already amongst our various Branches and Divisions.
After extensive discussions between Bill Hedges, John Fletcher, myself, and representatives of IMechE, l am delighted to say the new 10yr ICorr/IAR Training agreement was signed on 6th January 2023 by both parties, see later in this issue.
The Birmingham 1-Day conference on February 9th brought together many of our ICorr award winners, several of our sustaining companies and training providers, for some truly excellent presentations in the splendid setting of the City Chambers. A report on this can be found in the local branch news section.
Another development, now approved by Council, is the new Yong ICorr 8-week summer internship, established in honour of Professor Anne Neville, who sadly passed away in 2022. This new scheme commencing in 2024, will provide the opportunity for undergraduate students to experience corrosion research, initially in the Institute of Functional Surfaces, University of Leeds, under the supervision of Dr Joshua Owen and Prof Richard Barker, thereafter rotating to other Universities. The internship aims to inspire high achieving undergraduate students into careers in the field of corrosion.
Finally, but not least, we are looking to investigate, and fully research in Q2, whether a direct ICorr CEng offering can be progressed over the short to medium term. It is believed that (resources/volunteers permitting) ICorr CEng Direct would form a key element of ICorr membership growth going forwards, and would give greater prestige to the Institute, and help retain our existing members. It is proposed that a sub-committee of PAC be established under Vice President Yunnan Gao, working alongside David Harvey and Anthony Setiadi. Also aligned to our goals has been the recent work of our ICorr Awards Committee, with preparation of nominations of ICorr members for CSD, EFC and IOM3 awards currently ongoing.
Nick Smart, after several years of service has now stepped down from the committee. The new CED chair, Danny Burkle, has kindly volunteered to take up these duties, and we welcome him on board. We offer our thanks to Nick whose past support is highly appreciated.
A reminder that April 27th will take us to the Annual CED Working Day event at NPL Teddington, entitled ‘Corrosion Prevention in the 21st Century: Learning from the Past to protect the Future’, and June 22nd and 23rd will feature our main 2-day Sustainability and Renewables conference for NE Branch. August 29th will again see Aberdeen host its well-respected annual 1-day Corrosion Awareness event. For all events, please check regularly:
https://www.icorr.org/events/month/2023-04/
Please contact me on any aspect of the Institute’s work at: president@icorr.org
For anyone who has not yet renewed their membership, do please liaise with Institute of Corrosion HQ, at admin@icorr.org, who will be happy to help you, especially if your contact details have recently changed.
With my very best wishes to you all.
Stephen Tate
President: Institute of Corrosion